Stretch forming die with composite structure and manufacturing method of stretch forming die
A composite structure and die-casting technology, which is applied in the direction of manufacturing tools, metal processing equipment, forming tools, etc., can solve the problems that cannot meet the requirements of surface quality, cannot use the precise inspection of the geometric accuracy of the full surface, shape inspection and manufacturing basis, etc. Achieve the effects of eliminating skin bruises, light weight, and reducing total weight
- Summary
- Abstract
- Description
- Claims
- Application Information
AI Technical Summary
Problems solved by technology
Method used
Image
Examples
Embodiment 1
[0063] A drawing die of a composite structure includes an upper die assembly 2 and a lower die assembly 1, the upper die assembly 2 and the lower die assembly 1 are connected through a guide positioning device assembly 4, and the upper die assembly 2 is located at Above the lower mold assembly 1 , the upper surface of the lower mold assembly 1 is provided with a skin component positioning hole 1.5 hole making device assembly, and at least two earring hooks 5 are provided on the side of the lower mold assembly 1 .
Embodiment 2
[0065]A drawing die of a composite structure includes an upper die assembly 2 and a lower die assembly 1, the upper die assembly 2 and the lower die assembly 1 are connected through a guide positioning device assembly 4, and the upper die assembly 2 is located at Above the lower mold assembly 1 , the upper surface of the lower mold assembly 1 is provided with a skin component positioning hole 1.5 hole making device assembly, and at least two earring hooks 5 are provided on the side of the lower mold assembly 1 .
[0066] The lower mold assembly 1 includes a lower mold cast aluminum base 1.1, the upper surface of the lower mold cast aluminum base 1.1 is provided with a wave-shaped lower mold cuttable resin surface layer, and the lower mold can cut the resin mold surface layer The surface inflection point line 1.3, the surface engraved line and the mark and the positioning hole 1.5 of the skin part are respectively arranged on the top, and the edge of the lower mold that can cut ...
Embodiment 3
[0072] A method for manufacturing a drawing die of a composite structure, characterized in that:
[0073] design:
[0074] The first step: Design the lower mold to cut the resin surface layer;
[0075] The specific steps are: extract the outline of the skin part from the theoretical surface of the aircraft or the surface of the digital model of the process 1.4 The profile of the area within 10mm to 30mm along the periphery is used as the basic profile, which is determined by increasing the size of the part blank by 100mm to 200mm on one side Design the transitional surface between the maximum shape and the basic shape; then adjust the shape, determine the best drawing direction, and ensure that the heights of each protrusion are equal; then design the drawing angles and rounding corners on both sides , draw angle 70°-80°, draw fillet greater than R20mm and keep smooth and streamlined; then extract skin part outline 1.4, design part allowance line, positioning lug, first casti...
PUM
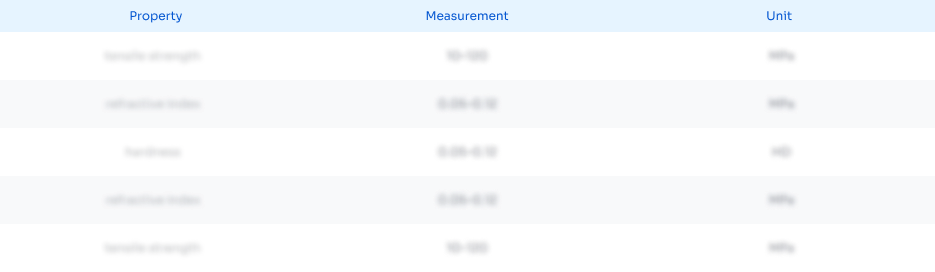
Abstract
Description
Claims
Application Information

- R&D
- Intellectual Property
- Life Sciences
- Materials
- Tech Scout
- Unparalleled Data Quality
- Higher Quality Content
- 60% Fewer Hallucinations
Browse by: Latest US Patents, China's latest patents, Technical Efficacy Thesaurus, Application Domain, Technology Topic, Popular Technical Reports.
© 2025 PatSnap. All rights reserved.Legal|Privacy policy|Modern Slavery Act Transparency Statement|Sitemap|About US| Contact US: help@patsnap.com