High-speed milling cutter abrasion vision in-place monitoring system and method
A technology for tool wear and high-speed milling, applied in the field of inspection, can solve the problems of complex shape of milling cutter, low imaging accuracy, light source scattering, etc., and achieve the effects of accurate monitoring, high image acquisition quality and less scattering
- Summary
- Abstract
- Description
- Claims
- Application Information
AI Technical Summary
Problems solved by technology
Method used
Image
Examples
Embodiment Construction
[0026] In order to better understand the present invention, the technical solution of the present invention will be further described below in conjunction with the description of the drawings and specific embodiments, see Figure 1 to Figure 9 .
[0027] The high-speed milling tool wear vision on-site monitoring system implemented according to the present invention includes a manipulator, which is a six-degree-of-freedom manipulator, which can teach and learn according to different detection positions and assembly positions, and store the optimal path coordinates for reproduction. The base of the manipulator is fixed on the ground, and the end of the manipulator is equipped with a clamp for clamping the lens. In order to facilitate the adjustment of the position of the lens, the clamp adopts a pneumatic clamp. The use of the six-degree-of-freedom manipulator makes it possible to monitor the tool stop gap in situ, and the system flexibility is enhanced.
[0028] In order to ob...
PUM
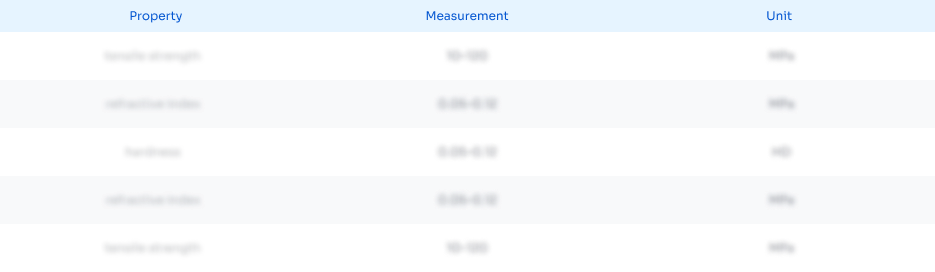
Abstract
Description
Claims
Application Information

- R&D Engineer
- R&D Manager
- IP Professional
- Industry Leading Data Capabilities
- Powerful AI technology
- Patent DNA Extraction
Browse by: Latest US Patents, China's latest patents, Technical Efficacy Thesaurus, Application Domain, Technology Topic, Popular Technical Reports.
© 2024 PatSnap. All rights reserved.Legal|Privacy policy|Modern Slavery Act Transparency Statement|Sitemap|About US| Contact US: help@patsnap.com