Manufacturing method for bottle
A production method and bottle technology, applied in glass production, glass blowing-blowing molding machines, etc., can solve problems such as broken waist, glass bottles are easy to break, and reduce the quality of glass bottles, so as to prevent broken waists, promote melting and clarification, The effect of reducing the production cost
- Summary
- Abstract
- Description
- Claims
- Application Information
AI Technical Summary
Problems solved by technology
Method used
Image
Examples
Embodiment 1
[0032] Embodiment 1 is basically as attached figure 1 Shown: the preliminary model, including the mold box 3, the feed pipe 5 and the partition 4, the partition 4 divides the mold box 3 into the upper scavenging chamber 6 and the lower preliminary chamber 7; the bottom of the preliminary chamber 7 A bulkhead 70 is detachably connected to seal the initial chamber 7; one end of the feed pipe 5 is fixed on the partition 4 and communicates with the initial chamber 7, and the other end of the feed pipe 5 passes through the scavenging chamber 6 and extends to Outside the scavenging chamber 6; the place where the feed pipe 5 is connected to the top of the scavenging chamber 6 is provided with a sealing ring, and a circular bump 56 is arranged below the sealing ring, so that the top of the scavenging chamber 6 is supported on the circular bump 56 , and be connected with the mold box 3 in rotation. Such as figure 2As shown, several blades 60 are arranged in the scavenging chamber 6,...
Embodiment 2
[0039] The difference between this embodiment and embodiment 1 is:
[0040] ①Material preparation: Mix the raw materials and grind them to 100 mesh to obtain a blank, 13 parts of quartz sand, 6 parts of calcite, 4 parts of nepheline, 9 parts of feldspar, 16 parts of cullet, and 3 parts of fluorite;
[0041] ② Melting: Heating the billet to 1350°C to obtain liquid glass. During the heating process, 110KHZ ultrasonic vibration is used to vibrate the billet, and the liquid glass is transferred to the liquid storage tank 2 .
Embodiment 3
[0043] The difference between this embodiment and embodiment 1 is:
[0044] ①Material preparation: Mix the raw materials and grind them to 120 mesh to obtain a blank, 15 parts of quartz sand, 8 parts of calcite, 5 parts of nepheline, 10 parts of feldspar, 18 parts of cullet, and 5 parts of fluorite;
[0045] ② Melting: Heating the billet to 1500°C to obtain liquid glass. During the heating process, use 130KHZ ultrasonic vibration to vibrate the billet to transfer the liquid glass to the liquid storage tank 2 .
PUM
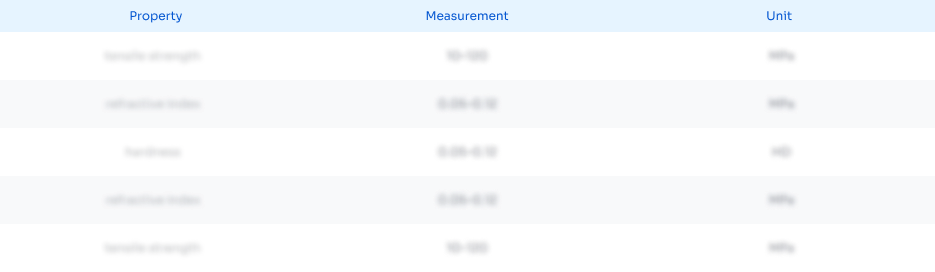
Abstract
Description
Claims
Application Information

- R&D
- Intellectual Property
- Life Sciences
- Materials
- Tech Scout
- Unparalleled Data Quality
- Higher Quality Content
- 60% Fewer Hallucinations
Browse by: Latest US Patents, China's latest patents, Technical Efficacy Thesaurus, Application Domain, Technology Topic, Popular Technical Reports.
© 2025 PatSnap. All rights reserved.Legal|Privacy policy|Modern Slavery Act Transparency Statement|Sitemap|About US| Contact US: help@patsnap.com