Plywood molding system
A technology of sheet material and forming area, which is applied in the field of forming system of plywood, can solve the problems of easy expansion and contraction deformation, high energy consumption, and insufficient compactness of pressing, and achieves high fire and flame retardancy, improved production efficiency, and realization of pressing conditions Effect
- Summary
- Abstract
- Description
- Claims
- Application Information
AI Technical Summary
Problems solved by technology
Method used
Image
Examples
Embodiment Construction
[0028] The scheme of this application is further described in conjunction with the accompanying drawings as follows:
[0029] See attached Figure 1-4 , a molding system for plywood, including a transport stacking area 1, a blank forming area 2, and a clamping and holding area 3 connected in sequence.
[0030] First, the conveying stacking area 1 includes a veneer conveying line 11, a laying line 10, and a gluing machine 12 arranged on the veneer conveying line 11 and the laying line 10, and the veneer is processed by the gluing machine 12. Glue is applied and the veneer 13 after gluing is conveyed to the laying line 10 through the veneer conveying line 11 to be stacked and conveyed.
[0031] Further, the single board 13 includes a head board, a horizontal board, a vertical board and a tail board.
[0032] The veneer conveying line 11 comprises a horizontal plate conveying line 111, a vertical plate conveying line 112, and a tail plate conveying line 113. The vertical versi...
PUM
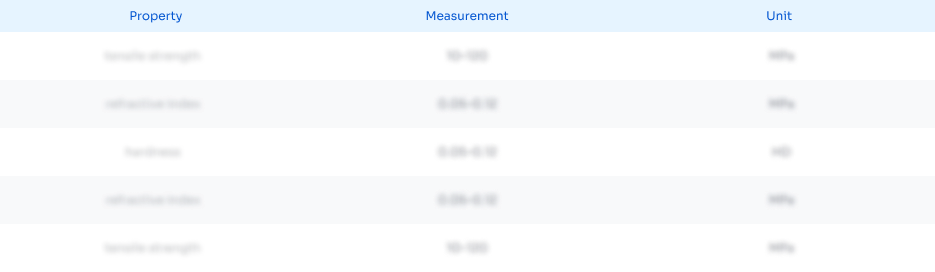
Abstract
Description
Claims
Application Information

- R&D
- Intellectual Property
- Life Sciences
- Materials
- Tech Scout
- Unparalleled Data Quality
- Higher Quality Content
- 60% Fewer Hallucinations
Browse by: Latest US Patents, China's latest patents, Technical Efficacy Thesaurus, Application Domain, Technology Topic, Popular Technical Reports.
© 2025 PatSnap. All rights reserved.Legal|Privacy policy|Modern Slavery Act Transparency Statement|Sitemap|About US| Contact US: help@patsnap.com