Plastic suction forming all-in-one machine
A technology of blister forming and all-in-one machine, which is applied in metal processing and other fields, can solve problems such as complex structure, poor efficiency, and power consumption, and achieve the effect of reasonable and simple structural design, improving complex structure, and improving poor efficiency
- Summary
- Abstract
- Description
- Claims
- Application Information
AI Technical Summary
Problems solved by technology
Method used
Image
Examples
Embodiment Construction
[0027] reference Figure 1 to Figure 11 It can be seen that the present invention: a blister molding integrated machine, including an extruding mechanism 1, a molding mechanism 2, a receiving mechanism 3, and a main controller 4. The molding mechanism 2 includes a molding machine punching, the molding mechanism 2 and The receiving mechanism 3 is installed on the frame 5. The forming mechanism 2 includes a forming base 6, an upper mold 7 and a lower mold 8 with a cavity installed on the frame 5. The lower end surface of the base 6 is connected There are screw rod I 61 and sliding grooves 62 located on both sides of the screw rod I 61, the frame 5 is provided with a guide rail 63 that cooperates with the sliding groove 62, and the base 5 is provided with a lower mold driving mechanism for connecting and driving the lower mold 8 81. The lower mold driving mechanism 81 includes a screw rod Ⅱ 66 arranged on the base 6, a fixed piece 82 with a hole and a connecting shaft structure 85...
PUM
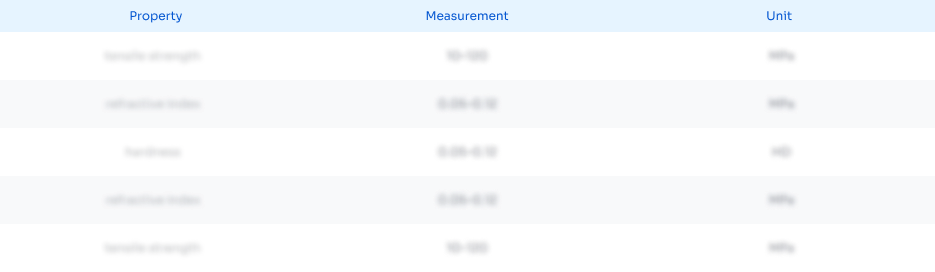
Abstract
Description
Claims
Application Information

- Generate Ideas
- Intellectual Property
- Life Sciences
- Materials
- Tech Scout
- Unparalleled Data Quality
- Higher Quality Content
- 60% Fewer Hallucinations
Browse by: Latest US Patents, China's latest patents, Technical Efficacy Thesaurus, Application Domain, Technology Topic, Popular Technical Reports.
© 2025 PatSnap. All rights reserved.Legal|Privacy policy|Modern Slavery Act Transparency Statement|Sitemap|About US| Contact US: help@patsnap.com