Injection molding machine super-thick large piece pouring system and pouring technology thereof
A pouring system and injection molding machine technology, applied in the direction of manufacturing tools, metal processing equipment, casting molding equipment, etc., can solve the problems affecting the use of recycled sand, cumbersome on-site preparation work, and affecting the quality of molten iron, so as to improve the operating efficiency of employees and reduce The risk of scrapping and the effect of improving the purity of molten iron
- Summary
- Abstract
- Description
- Claims
- Application Information
AI Technical Summary
Problems solved by technology
Method used
Image
Examples
specific Embodiment
[0014] Stable filling is a factor that must be considered in the design of the gating system. As long as the above factors are guaranteed, the runner can be fully used to avoid slag. Therefore, after canceling the filter screen and ceramic tube, the pouring system must be reasonably designed to control the flow rate of molten iron in the pouring system. On the one hand, the runner is used to avoid slag without slag formation, and on the other hand, the flow rate of the inner runner is controlled.
[0015] Therefore, based on the above principles, the present invention designs double slag-avoiding runners and adopts a thinner inner runner, such as figure 1 As shown, a gating system for super-thick and large parts of an injection molding machine includes a casting 1, a sprue 2, a first runner 3, a thin runner 4, a second runner 5 and an inner runner 6. The casting 1 is provided with a sprue 2, the sprue 2 communicates with the first runner 3, and the end of the first runner 3 is...
PUM
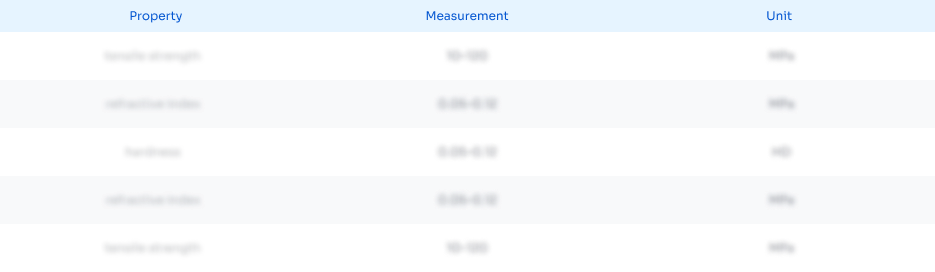
Abstract
Description
Claims
Application Information

- R&D
- Intellectual Property
- Life Sciences
- Materials
- Tech Scout
- Unparalleled Data Quality
- Higher Quality Content
- 60% Fewer Hallucinations
Browse by: Latest US Patents, China's latest patents, Technical Efficacy Thesaurus, Application Domain, Technology Topic, Popular Technical Reports.
© 2025 PatSnap. All rights reserved.Legal|Privacy policy|Modern Slavery Act Transparency Statement|Sitemap|About US| Contact US: help@patsnap.com