Processing technique of anti-rust and anti-corrosion hammer head
A processing technology and anti-corrosion technology, applied in the direction of coating, epoxy resin coating, etc., can solve the problem of hammer head easy to rust and corrode, break or crack, and form accident sources, so as to improve the anti-rust and anti-corrosion performance, manufacturing The effect of low cost and simple process
- Summary
- Abstract
- Description
- Claims
- Application Information
AI Technical Summary
Problems solved by technology
Method used
Examples
Embodiment Construction
[0016] The technical solutions of the present invention will be clearly and completely described below in conjunction with specific embodiments.
[0017] An anti-rust and anti-corrosion hammer head processing technology disclosed by the present invention specifically includes the following steps:
[0018] a. Semi-finished product processing, select medium-carbon alloy steel as the raw material of the hammer head, process the raw material through the mold according to the size specification, and obtain the semi-finished product;
[0019] b. Heat preservation and cooling, heat preservation and cooling in the bell furnace, first control the heat preservation temperature to 600~700°C, the heat preservation time is 5~9h, after heat preservation, the cooling temperature with the furnace body is below 250°C;
[0020] c, surface treatment, carry out phosphating treatment to the screw section of the hammer head semi-finished product after annealing;
PUM
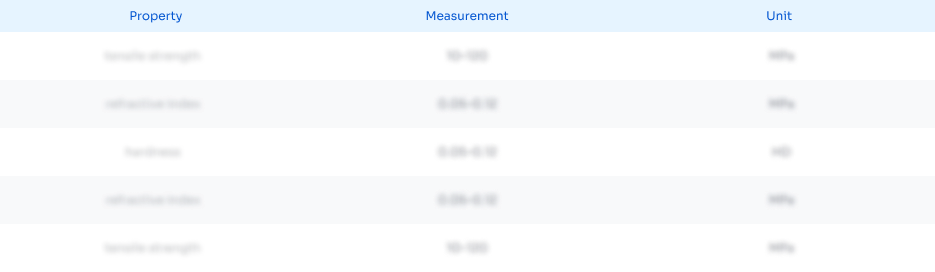
Abstract
Description
Claims
Application Information

- Generate Ideas
- Intellectual Property
- Life Sciences
- Materials
- Tech Scout
- Unparalleled Data Quality
- Higher Quality Content
- 60% Fewer Hallucinations
Browse by: Latest US Patents, China's latest patents, Technical Efficacy Thesaurus, Application Domain, Technology Topic, Popular Technical Reports.
© 2025 PatSnap. All rights reserved.Legal|Privacy policy|Modern Slavery Act Transparency Statement|Sitemap|About US| Contact US: help@patsnap.com