Achievement method for predicting laser welding deformation
A technology of laser welding and realization method, which is applied in welding equipment, auxiliary welding equipment, welding/cutting auxiliary equipment, etc., can solve the problem of inability to accurately fit the morphology of the molten pool area at the weld and control the morphology of the weld pool area of the weld. , Welding deformation simulation effect is poor, etc.
- Summary
- Abstract
- Description
- Claims
- Application Information
AI Technical Summary
Problems solved by technology
Method used
Image
Examples
Embodiment Construction
[0038] Such as figure 1 As shown, this embodiment includes the following steps:
[0039] 1) Weld the test workpiece and measure the deformation of the workpiece after welding.
[0040] Such as figure 2 As shown, the test workpiece is the B-pillar area panel in the automobile body, that is, the laser welding method is used to weld the B-pillar inner panel and the B-pillar reinforcement. The reinforced version of the B-pillar and the inner panel of the B-pillar are the test workpieces. The test workpiece is optically scanned to obtain the geometric shape of the test workpiece, which is used to establish the finite element model of the test workpiece.
[0041] Such as image 3 As shown, after the test workpiece is welded, three-dimensional optical scanning is carried out to obtain the deformation of the test workpiece after welding.
[0042] 2) Conduct metallographic microscopic observation of the weld area to obtain the geometric morphology of the molten pool area.
[004...
PUM
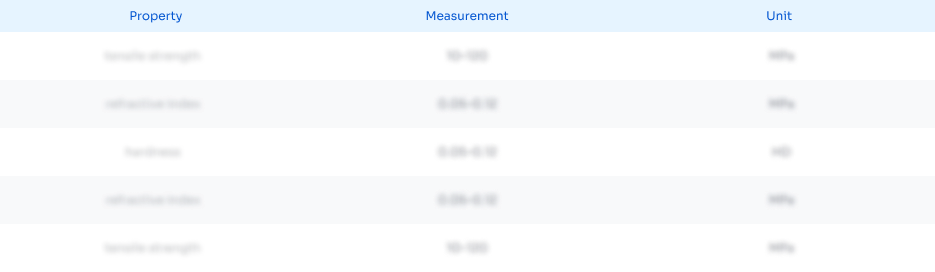
Abstract
Description
Claims
Application Information

- R&D
- Intellectual Property
- Life Sciences
- Materials
- Tech Scout
- Unparalleled Data Quality
- Higher Quality Content
- 60% Fewer Hallucinations
Browse by: Latest US Patents, China's latest patents, Technical Efficacy Thesaurus, Application Domain, Technology Topic, Popular Technical Reports.
© 2025 PatSnap. All rights reserved.Legal|Privacy policy|Modern Slavery Act Transparency Statement|Sitemap|About US| Contact US: help@patsnap.com