Method for producing diphosgene or triphosgene from phosgene
A technology of triphosgene and diphosgene, which is applied in the direction of carbonyl chloride, etc., can solve the problems of complex catalyst screening process, equipment corrosion, and long time, and achieve the effects of avoiding side reactions and equipment corrosion, prolonging service life, and preventing poisoning
- Summary
- Abstract
- Description
- Claims
- Application Information
AI Technical Summary
Problems solved by technology
Method used
Image
Examples
Embodiment 1
[0026] Example 1: A 35% triphosgene solution was configured in a jacketed enamel stirred tank provided with an exhaust protection port, the solvent was diethyl isophthalate, and the temperature of the solution was controlled to be 55°C. Stop stirring after complete dissolution, and transfer all the solution to the enamel-jacketed buffer tank below. The solution is pumped from the buffer tank to the molecular sieve purifier to remove impurities, and the purified triphosgene solution is sent to the bottom of the tubular fixed-bed catalytic reactor and passes through the reactor from bottom to top. The reactor temperature was controlled to be 65° C., and the residence time was 50 minutes. The gas-liquid two-phase medium overflows from the top of the reactor. After being treated by the rectification tower and liquid separator, the solvent returns to the jacketed enamel stirring tank for continued use. The water is discharged intermittently, and the phosgene is sent from the top of...
Embodiment 2
[0027] Example 2: A 50% triphosgene solution was prepared in a jacketed enamel stirred tank provided with an exhaust protection port, the solvent was o-dichlorobenzene, and the temperature of the solution was controlled to be 80°C. Stop stirring after complete dissolution, and transfer all the solution to the enamel-jacketed buffer tank below. The solution is pumped from the buffer tank to a high-speed centrifugal purifier, and the purified triphosgene solution is sent to the bottom of the tubular fixed-bed catalytic reactor and passes through the reactor from bottom to top. The temperature of the reactor was controlled to be 90° C., and the residence time was 45 minutes. The gas-liquid two-phase medium overflows from the top of the reactor. After being treated by the rectification tower and liquid separator, the solvent returns to the jacketed enamel stirring tank for continued use. The water is discharged intermittently, and the phosgene is sent from the top of the rectifica...
Embodiment 3
[0028] Example 3: A 50% triphosgene solution was prepared in a jacketed enamel stirred tank provided with an exhaust protection port, the solvent was chlorobenzene, and the temperature of the solution was controlled to be 80°C. Stop stirring after complete dissolution, and transfer all the solution to the enamel-jacketed buffer tank below. The solution is pumped from the buffer tank to the filter purifier, and the purified triphosgene solution is sent to the bottom of the tubular fixed-bed catalytic reactor and passes through the reactor from bottom to top. The reactor temperature was controlled to be 100° C., and the residence time was 30 minutes. The gas-liquid two-phase medium overflows from the top of the reactor. After being treated by the rectification tower and liquid separator, the solvent returns to the jacketed enamel stirring tank for continued use. The water is discharged intermittently, and the phosgene is sent from the top of the rectification tower to the Phosg...
PUM
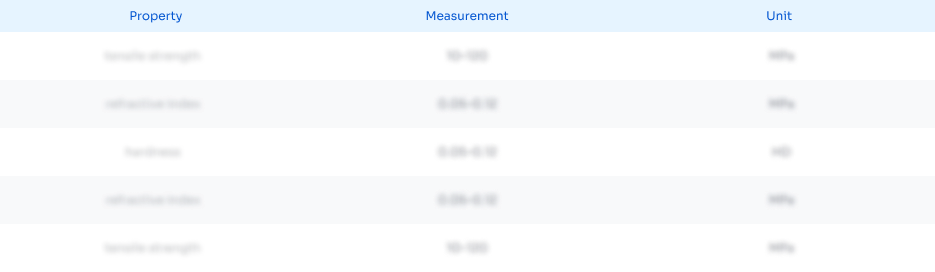
Abstract
Description
Claims
Application Information

- Generate Ideas
- Intellectual Property
- Life Sciences
- Materials
- Tech Scout
- Unparalleled Data Quality
- Higher Quality Content
- 60% Fewer Hallucinations
Browse by: Latest US Patents, China's latest patents, Technical Efficacy Thesaurus, Application Domain, Technology Topic, Popular Technical Reports.
© 2025 PatSnap. All rights reserved.Legal|Privacy policy|Modern Slavery Act Transparency Statement|Sitemap|About US| Contact US: help@patsnap.com