Six-dimensional piezoelectric vibration energy collector
An energy harvester, electric vibration technology, applied in the direction of generator/motor, piezoelectric effect/electrostrictive or magnetostrictive motor, electrical components, etc., can solve problems such as large energy consumption, dead point, component wear and so on , to achieve high energy collection efficiency, easy processing and assembly, and reasonable structural settings
- Summary
- Abstract
- Description
- Claims
- Application Information
AI Technical Summary
Problems solved by technology
Method used
Image
Examples
Embodiment 1
[0025] Such as figure 1 A six-dimensional piezoelectric vibration energy harvester shown includes a base 1, a plurality of flexible beams 2, a plurality of outrigger assemblies 5 and an inertial mass set above the base 1, the base 1 and the inertial mass There are gaps between them, a plurality of flexible beams 2 are distributed in a circular array, and the outrigger components 5 correspond to the flexible beams 2 one by one; the flexible beams 2 are elongated structures, and the roots of the flexible beams 2 are fixedly connected to the base 1 to form Cantilever beam structure, the free end of the flexible beam 2 is fixedly connected to one end of the outrigger assembly 5, the other end of the outrigger assembly 5 is fixedly connected to the inertial mass, and there is a clamp between the outrigger assembly 5 and the flexible beam 2 connected to it. Angle; in order to transmit the vibration of the inertial mass as much as possible to the flexible beam 2 through the outrigger...
Embodiment 2
[0033] Such as figure 2 As shown, the difference between the second embodiment and the first embodiment is that the flexible beam 2 in the second embodiment is a thin plate-shaped elongated structure, and the flexible beam 2 of this structure can also be placed in the The roots undergo a relatively large mechanical deformation.
Embodiment 3
[0035] Such as image 3 As shown, the difference between the third embodiment and the first embodiment is that six flexible beams 2 are fixedly connected to the base 1 in the third embodiment, and the angle between two adjacent flexible beams 2 is 60 degrees.
PUM
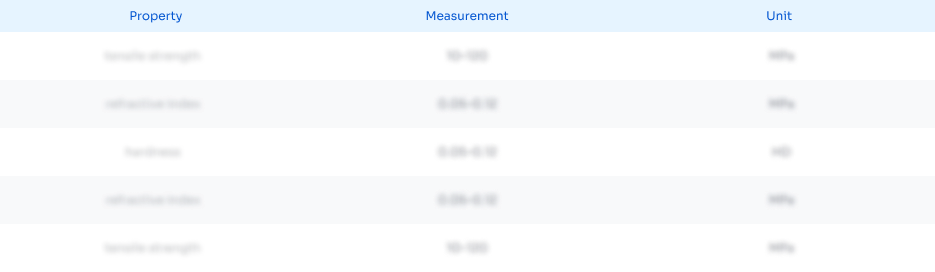
Abstract
Description
Claims
Application Information

- R&D
- Intellectual Property
- Life Sciences
- Materials
- Tech Scout
- Unparalleled Data Quality
- Higher Quality Content
- 60% Fewer Hallucinations
Browse by: Latest US Patents, China's latest patents, Technical Efficacy Thesaurus, Application Domain, Technology Topic, Popular Technical Reports.
© 2025 PatSnap. All rights reserved.Legal|Privacy policy|Modern Slavery Act Transparency Statement|Sitemap|About US| Contact US: help@patsnap.com