Data-driven information modeling method for complex electromechanical system in process industry
An electromechanical system and process industry technology, applied in electrical digital data processing, special data processing applications, instruments, etc., can solve problems such as specific applications and noise sensitivity without complex electromechanical system information modeling in process industry, and achieve auxiliary scientific maintenance. The effect of maintaining and improving the level of digital monitoring
- Summary
- Abstract
- Description
- Claims
- Application Information
AI Technical Summary
Problems solved by technology
Method used
Image
Examples
Embodiment Construction
[0049] The present invention will be further explained below in conjunction with specific embodiments and accompanying drawings.
[0050] see figure 1 , the present invention comprises the following steps:
[0051] 1) Obtain the monitoring data of the complex electromechanical system, and establish a high-dimensional historical monitoring data set. The historical monitoring data set is an n-dimensional monitoring time series matrix: this step is the original data collection step, and the process industry complex electromechanical system monitoring system (DCS, SCADA etc.), from the historical monitoring data of n sensors, the original data set is extracted at the same sampling frequency as the monitoring time series matrix, and an n-dimensional monitoring time series matrix D is obtained:
[0052]
[0053] where: X i is the i-th sample point in the matrix; d i,j is the j-th attribute value in the i-th sample point, and each column in the matrix is the monitoring time s...
PUM
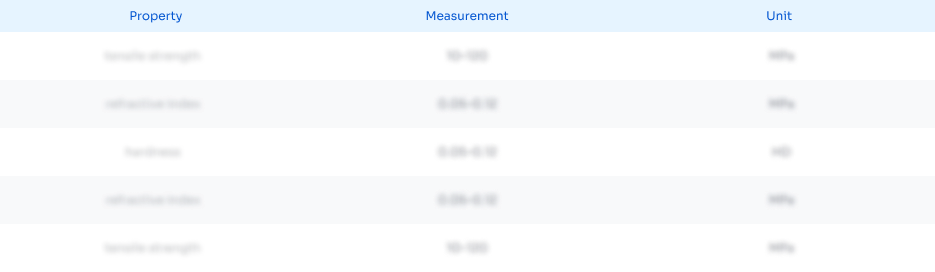
Abstract
Description
Claims
Application Information

- R&D
- Intellectual Property
- Life Sciences
- Materials
- Tech Scout
- Unparalleled Data Quality
- Higher Quality Content
- 60% Fewer Hallucinations
Browse by: Latest US Patents, China's latest patents, Technical Efficacy Thesaurus, Application Domain, Technology Topic, Popular Technical Reports.
© 2025 PatSnap. All rights reserved.Legal|Privacy policy|Modern Slavery Act Transparency Statement|Sitemap|About US| Contact US: help@patsnap.com