Method for improving dyeing property of natural dye
A technology of natural dyes and dyeing properties, applied in the field of textile chemistry, can solve the problems of poor color fastness to washing, low dye exhaustion rate, etc. Effect
- Summary
- Abstract
- Description
- Claims
- Application Information
AI Technical Summary
Problems solved by technology
Method used
Image
Examples
Embodiment 1
[0020] Example 1: At 23°C, 0.02g (1% o.m.f), 0.04g (2% o.m.f), 0.06g (3% o.m.f), and 0.10g (5% o.m.f) natural dye gardenia blue and cationic dye 0.3g (15% o.m.f) of color fixing agent was made into 70mL dye liquor (bath ratio 1:35), and after stirring until uniform, 2g of cotton yarn was immersed in the dye liquor, and dyed in a dyeing machine at room temperature for 15 Minutes, let the natural dye gardenia blue and cationic dye fixing agent be evenly and slowly absorbed on the cotton yarn. Then heat it up to 80°C at a heating rate of 2°C / min, keep it warm for 45 minutes, then drop it to 23°C at a cooling rate of 5°C / min, take out the dyed cotton yarn and dry it in an oven at 90°C. Wash the dyed cotton yarn after drying in 70ml washing solution containing 2g / L non-ionic detergent at 70°C for 15min, and finally dry it to complete the dyeing.
[0021] A spectrophotometer was used to detect the absorbance of the dyeing solution before dyeing, the dyeing residue after dyeing and ...
Embodiment 2
[0024] Example 2: At 23°C, add 0.06g (3% o.m.f) natural dye gardenia blue and 0g, 0.1g (5% o.m.f), 0.2g (10% o.m.f), 0.3g (15% o.m.f) and 0.4 g (20% o.m.f) cationic dye fixing agent to prepare 70mL (bath ratio 1:35) of dye liquor, stir until uniform, immerse 2g of cotton yarn into the dye liquor, and dye in the dyeing machine at room temperature For 15 minutes, the natural dye gardenia blue and the cationic dye fixing agent are evenly and slowly absorbed on the cotton yarn. Then heat it up to 80°C at a heating rate of 2°C / min, keep it warm for 45 minutes, then drop it to 23°C at a cooling rate of 5°C / min, take out the dyed cotton yarn and dry it in an oven at 90°C. Wash the dyed cotton yarn after drying in 70ml washing solution containing 2g / L non-ionic detergent at 70°C for 15min, and finally dry it to complete the dyeing.
[0025] Use a spectrophotometer to detect the absorbance of the dyeing solution before dyeing, the dyeing residue after dyeing and the washing solution, ...
Embodiment 3
[0029] Example 3: At 23°C, 0.06g (3% o.m.f) of natural dye gardenia blue and 0.3g (15% o.m.f) of cationic dye fixing agent were made into 70mL (bath ratio 1:35) of the dye solution, After stirring until uniform, immerse 2g of cotton yarn in the dyeing solution, and dye in the dyeing machine at room temperature for 15 minutes, so that the natural dye gardenia blue and cationic dye fixing agent are evenly and slowly absorbed on the cotton yarn. Then heat it up to 80°C at a heating rate of 2°C / min, keep it warm for 30, 45, 60 and 90 minutes, then drop it to 23°C at a cooling rate of 5°C / min, take out the dyed product and dry it in an oven at 90°C Dry. Wash the dyed cotton yarn after drying in 70ml washing solution containing 2g / L non-ionic detergent at 70°C for 15min, and finally dry it to complete the dyeing.
[0030] Use a spectrophotometer to detect the absorbance of the dyeing solution before dyeing, the dyeing residue after dyeing and the washing solution, and calculate the...
PUM
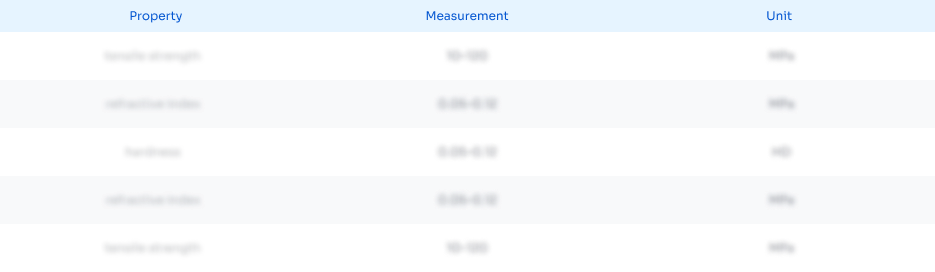
Abstract
Description
Claims
Application Information

- R&D Engineer
- R&D Manager
- IP Professional
- Industry Leading Data Capabilities
- Powerful AI technology
- Patent DNA Extraction
Browse by: Latest US Patents, China's latest patents, Technical Efficacy Thesaurus, Application Domain, Technology Topic, Popular Technical Reports.
© 2024 PatSnap. All rights reserved.Legal|Privacy policy|Modern Slavery Act Transparency Statement|Sitemap|About US| Contact US: help@patsnap.com