Extrusion breakdown method for high-temperature alloy cast ingot for turbine disc
A technology of superalloy and deformed superalloy, which is applied in metal extrusion, metal extrusion die, metal extrusion control equipment, etc., can solve the problems of wasting strategic alloy elements, low material utilization rate, and reducing metal utilization rate, etc. Achieve the effect of controllable grain refinement, improved raw material utilization, and low mold strength requirements
- Summary
- Abstract
- Description
- Claims
- Application Information
AI Technical Summary
Problems solved by technology
Method used
Image
Examples
Embodiment Construction
[0028] The technical scheme of the present invention will be described in further detail below in conjunction with accompanying drawing and embodiment:
[0029] See attached Figure 1~3 Shown, the superalloy in the extrusion billet opening method of the turbine disk superalloy ingot of the present invention is GH710, and the steps of the method are as follows:
[0030] Step 1, manufacture extrusion die, this extrusion die is a cylindrical structure, and the section of inner chamber 1 of extrusion die along center line 2 is trapezoidal; Extrusion die material selects K3 alloy for use, and specification is Φ200 * 300mm, in alloy Machining on the ingot, the angle between the side 3 of the trapezoidal section of the inner cavity 1 of the extrusion die along the center line 2 and the center line 2 is 20°, and the upper end of the inner cavity 1 of the extrusion die has a large opening The edge is processed with a ring-shaped vertical guide boss 4 that acts as a positioning functio...
PUM
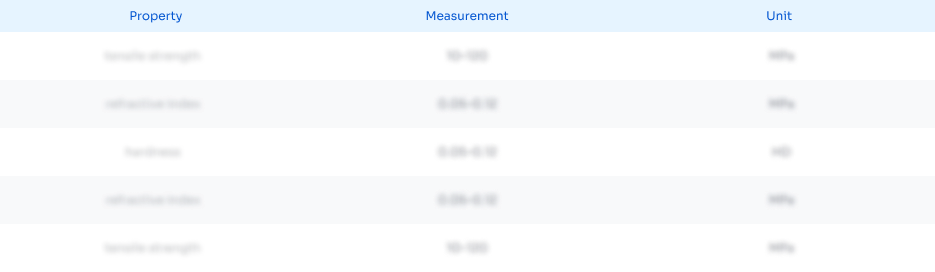
Abstract
Description
Claims
Application Information

- R&D
- Intellectual Property
- Life Sciences
- Materials
- Tech Scout
- Unparalleled Data Quality
- Higher Quality Content
- 60% Fewer Hallucinations
Browse by: Latest US Patents, China's latest patents, Technical Efficacy Thesaurus, Application Domain, Technology Topic, Popular Technical Reports.
© 2025 PatSnap. All rights reserved.Legal|Privacy policy|Modern Slavery Act Transparency Statement|Sitemap|About US| Contact US: help@patsnap.com