Asymmetric half-bridge flyback drive circuit
A driving circuit, asymmetric technology, applied in the direction of electrical components, adjusting electrical variables, high-efficiency power electronic conversion, etc., can solve the problems of difficult control of dead time, poor consistency of driving signals, and affecting the quality of driving waveforms, etc., to achieve working timing The effects of high consistency, improved driver consistency, and high timing consistency
- Summary
- Abstract
- Description
- Claims
- Application Information
AI Technical Summary
Problems solved by technology
Method used
Image
Examples
no. 1 example
[0032] image 3 The circuit diagram of the first embodiment is shown, including input voltages Vin+ and Vin-, a complementary PWM signal generator, a driving transformer T1, a driving transformer T2, and a series asymmetrical half-bridge flyback circuit. The complementary PWM generator can send out a signal with a variable pulse width in a certain dead zone interval; the drive transformer T1 includes the first DC blocking capacitor C1, the primary winding L1, the second DC blocking capacitor C2, the first diode D1, the secondary side winding L2, the third DC blocking capacitor C3, the secondary winding L3, and the second diode D2; the driving transformer T2 is composed of the fourth DC blocking capacitor C4, the primary winding L4, the fifth DC blocking capacitor C5, the secondary winding L5, The third diode D3, the sixth DC blocking capacitor C6, the secondary winding L6, and the fourth diode D4 are composed; the series asymmetrical half-bridge flyback circuit is composed of ...
no. 2 example
[0044] Figure 4 It is a circuit diagram of the second example, which is different from the first embodiment in that resistors R1 , R2 , R3 and R4 are driven in series at the gate of each switch tube respectively. The specific connection relationship is: one end of the resistor R1 is connected to the other end of C2 and the cathode of the diode D1 at the same time, and the other end of R1 is connected to the gate of the switching tube Q1; one end of the resistor R2 is connected to the other end of C3 and the cathode of the diode D2 at the same time, The other end of R2 is connected to the grid of the switch tube Q3; one end of the resistor R3 is connected to the other end of C5 and the cathode of the diode D3 at the same time, and the other end of R3 is connected to the grid of the switch tube Q2; one end of the resistor R4 is connected to the other end of C6 at the same time and the cathode of the diode D4, and the other end of R4 is connected to the gate of the switching tub...
no. 3 example
[0047] Figure 5 It is the circuit diagram of the third example. The difference from the first embodiment is that the asymmetrical half-bridge flyback circuit consists of three pairs connected in series and has six switching tubes. The driving transformer T1 and the driving transformer T2 are respectively composed of four sets of windings. On the basis of the first embodiment, the secondary winding L7, capacitor C7, diode D5, and switch Q5 of the transformer T1 are added; the secondary winding L8, capacitor C8, diode D6, and switch Q6 of the transformer T2 are added. The connection relationship of the newly added components is: the end of the same name of the secondary winding L7 is connected to one end of the capacitor C7, the other end of the capacitor C7 is respectively connected to the cathode of the diode D5 and the gate of the switching tube Q5, and the opposite end of the secondary winding L7 is respectively connected to The anode of the diode D5 is connected to the sou...
PUM
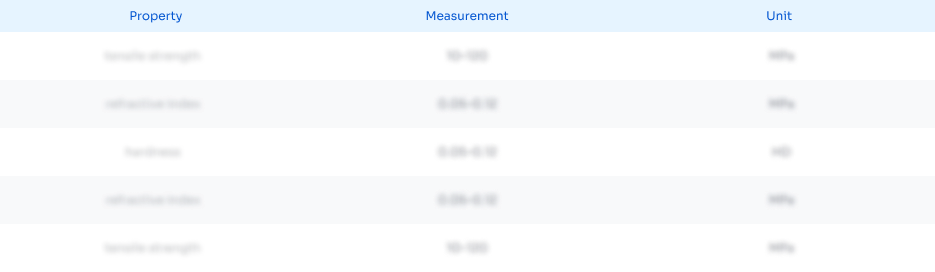
Abstract
Description
Claims
Application Information

- R&D Engineer
- R&D Manager
- IP Professional
- Industry Leading Data Capabilities
- Powerful AI technology
- Patent DNA Extraction
Browse by: Latest US Patents, China's latest patents, Technical Efficacy Thesaurus, Application Domain, Technology Topic, Popular Technical Reports.
© 2024 PatSnap. All rights reserved.Legal|Privacy policy|Modern Slavery Act Transparency Statement|Sitemap|About US| Contact US: help@patsnap.com