High bearing capacity steel pipe joint and manufacturing method
A production method and bearing capacity technology, applied in the direction of instruments, electrical digital data processing, computer-aided design, etc., can solve the problems of ring plate welding production difficulties, material waste, and welding processing difficulties, so as to improve economic and social benefits, The effect of saving material consumption and reducing force transmission distance
- Summary
- Abstract
- Description
- Claims
- Application Information
AI Technical Summary
Problems solved by technology
Method used
Image
Examples
Embodiment Construction
[0032] The present invention will be further described below in conjunction with accompanying drawing and specific embodiment: figure 1 , 2 As shown, a high-capacity steel pipe tower node described in the present invention is used to connect the main pipe 2 and a plurality of branch pipes 4 of the steel pipe tower. The gusset plate 3 of the component for transmitting force and preventing the instability of the ring plate is arranged in the area of the gusset plate 3 with a plurality of load-bearing circular ring plates 1 as the main force-bearing components, and each circular ring plate 1 is connected with the main pipe 2 and The gusset plate 3 is vertical and welded.
[0033] As shown in the figure, the branch pipe 4 and the gusset plate 3 are connected by welding, U-shaped plate 5 or cross plate; the gusset plate 3 is kept as a continuous plate, while the circular ring plate 1 is The gusset plate 3 is fixed on the gusset plate 3 by cutting first and then welding. The pos...
PUM
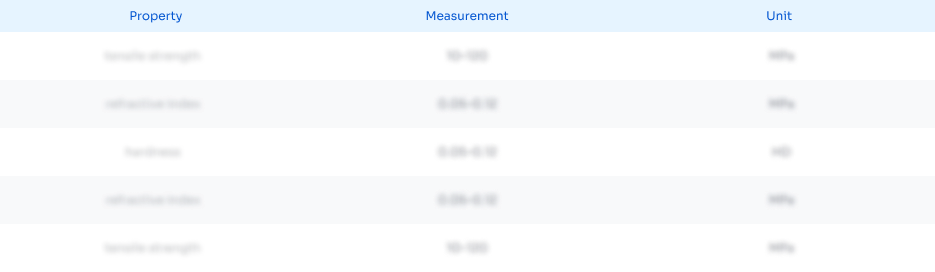
Abstract
Description
Claims
Application Information

- Generate Ideas
- Intellectual Property
- Life Sciences
- Materials
- Tech Scout
- Unparalleled Data Quality
- Higher Quality Content
- 60% Fewer Hallucinations
Browse by: Latest US Patents, China's latest patents, Technical Efficacy Thesaurus, Application Domain, Technology Topic, Popular Technical Reports.
© 2025 PatSnap. All rights reserved.Legal|Privacy policy|Modern Slavery Act Transparency Statement|Sitemap|About US| Contact US: help@patsnap.com