Heat exchanging plate, machining method and heat exchanger
A processing method and heat exchange plate technology, applied in the field of heat exchange plates and heat exchangers, can solve problems affecting system efficiency and economy, uneven flow distribution, increased compression power consumption, etc., to increase effective heat transfer area, save power consumption, and reduce the effect of channel resistance
- Summary
- Abstract
- Description
- Claims
- Application Information
AI Technical Summary
Problems solved by technology
Method used
Image
Examples
Embodiment Construction
[0034] In the embodiment of the present invention, the front and back sides of the same heat exchange plate are machined, chemically and laser etched to form a mesh including a graded flow channel 2 , a secondary flow channel 4 and a mesh between the graded flow channel 2 and the secondary flow channel 4 The vein-shaped fluid distribution structure of the flow channel 3 is used as a fluid heat transfer microchannel for heat exchange of fluids (such as supercritical fluids), and the positions of the vein-shaped heat transfer microchannels on the front and back of the same heat exchange plate correspond. Therefore, The heat transfer microchannel with the fractal feature of leaf veins produces more and more branches, which not only greatly increases the convective heat transfer area and enhances the convective heat transfer effect, but also uses the leaf vein bionic structure to reduce the flow resistance of the working fluid. On the premise of consumption, the working medium is t...
PUM
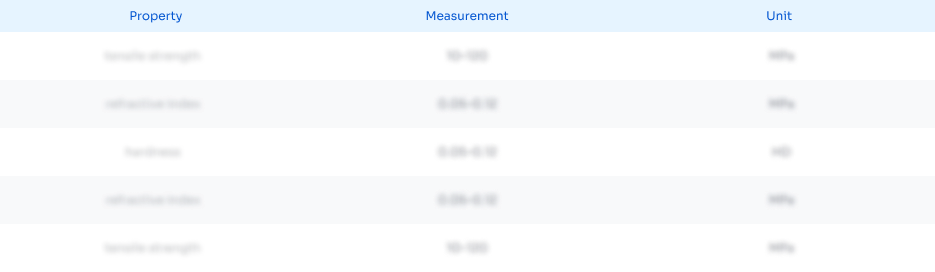
Abstract
Description
Claims
Application Information

- R&D
- Intellectual Property
- Life Sciences
- Materials
- Tech Scout
- Unparalleled Data Quality
- Higher Quality Content
- 60% Fewer Hallucinations
Browse by: Latest US Patents, China's latest patents, Technical Efficacy Thesaurus, Application Domain, Technology Topic, Popular Technical Reports.
© 2025 PatSnap. All rights reserved.Legal|Privacy policy|Modern Slavery Act Transparency Statement|Sitemap|About US| Contact US: help@patsnap.com