Method for assembling steel structure framework and composite lightweight floor slab module
A steel structure frame, composite technology, applied in building construction, building material processing, construction and other directions, can solve the problems of reducing construction work space, low construction efficiency, occupying more space, etc., to shorten the construction period and improve the construction. Speed, avoid the effect of secondary decoration
- Summary
- Abstract
- Description
- Claims
- Application Information
AI Technical Summary
Problems solved by technology
Method used
Image
Examples
Embodiment Construction
[0040] See attached Figure 1-8 A method for assembling a steel structure frame and a composite lightweight floor module, the method is based on a floor datum plane formed by the steel structure frame, and the method includes the following process steps:
[0041] 1) Manufacture floor modules for assembly according to architectural drawings 1: According to the preset connection parts and technical parameters of position and shape on the steel structure frame, used to manufacture floor modules for assembly 1. Process reserved process holes and equip on-site Connection fasteners for construction;
[0042] 2) The upper end surface of the load-bearing beam 3 in the steel structure frame forms the floor reference plane;
[0043] 3) Check the prefabricated steel column 2 and load-bearing beam 3 in the steel structure frame, the connecting parts, the connection position and the process assembly hole tolerance with the floor module 1, and prepare the adjusting gasket;
[0044] 4) Pos...
PUM
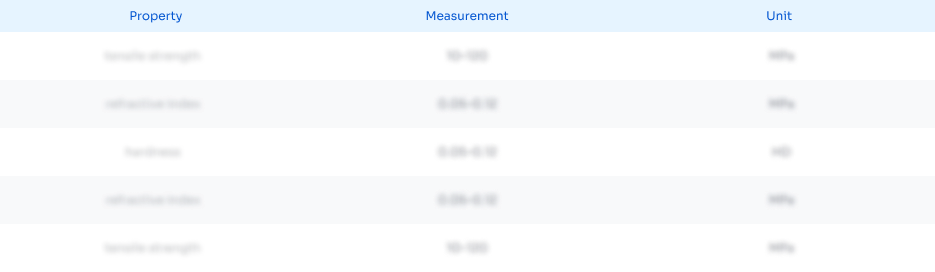
Abstract
Description
Claims
Application Information

- R&D Engineer
- R&D Manager
- IP Professional
- Industry Leading Data Capabilities
- Powerful AI technology
- Patent DNA Extraction
Browse by: Latest US Patents, China's latest patents, Technical Efficacy Thesaurus, Application Domain, Technology Topic, Popular Technical Reports.
© 2024 PatSnap. All rights reserved.Legal|Privacy policy|Modern Slavery Act Transparency Statement|Sitemap|About US| Contact US: help@patsnap.com