Method for recovering rhenium from high-sulfur high-arsenic unwieldiness lean rhenium slag
A difficult-to-treat, high-sulfur technology, applied in the direction of improving process efficiency, can solve the problems of difficult filtration of leachate, low rhenium leaching rate, and difficult treatment of produced copper and arsenic slag, so as to improve the level of comprehensive utilization and the recovery rate of rhenium High efficiency and low running cost
- Summary
- Abstract
- Description
- Claims
- Application Information
AI Technical Summary
Problems solved by technology
Method used
Image
Examples
Example Embodiment
[0017] Example 1
[0018] In this embodiment, the high-sulfur and high-arsenic refractory rhenium-poor slag contains 0.18% rhenium, 16.50% arsenic, 2.53% copper, 9.87% bismuth, and 62.85% sulfur based on the mass percentage of the rhenium-poor slag.
[0019] a. Weigh 500 g of the above-mentioned rhenium-poor slag, put it into a muffle furnace, heat it up to 260 ° C, and then feed it into air for oxidative roasting for 6 hours, and open the tail gas absorption and condensation device simultaneously; In terms of mass percentage, it contains 1.18% rhenium, 0.38% arsenic, 21.60% copper, 41.47% bismuth, and 0.8% sulfur;
[0020] b. Take the rhenium-rich slag in step a and carry out selective leaching under oxygen pressure, the leaching process is two-stage countercurrent leaching, and the leaching conditions are the same, wherein the leaching solvent is hydrogen peroxide, and the solid-liquid mass volume ratio is 3:1, and saturated sodium carbonate is used before leaching The pH v...
Example Embodiment
[0024] Example 2
[0025] In this embodiment, the high-sulfur and high-arsenic refractory rhenium-poor slag contains 0.18% rhenium, 18.49% arsenic, 2.65% copper, 10.60% bismuth, and 63.33% sulfur based on the mass percentage of the rhenium-poor slag.
[0026] a. Weigh 500 g of the above-mentioned rhenium-poor slag, put it into a muffle furnace, and feed air for oxidative roasting at 265 ° C for 6.5 hours, and open the exhaust gas absorption and condensation device at the same time; In percentage terms, it contains 1.19% rhenium, 0.41% arsenic, 23.34% copper, 44.09% bismuth, and 1.02% sulfur;
[0027] b. Take the rhenium-rich slag in step a and carry out selective leaching under oxygen pressure. The leaching process is two-stage countercurrent leaching, and the leaching conditions are the same. The leaching solvent is hydrogen peroxide, and the solid-liquid mass-volume ratio is 4:1. Before leaching, saturated sodium carbonate is used. The pH value of the solution was adjusted ...
Example Embodiment
[0031] Example 3
[0032] In this embodiment, the high-sulfur and high-arsenic refractory rhenium-poor slag contains 0.20% rhenium, 18.04% arsenic, 3.44% copper, 11.21% bismuth, and 63.30% sulfur in terms of the mass percentage of the rhenium-poor slag.
[0033] a. Weigh 500 g of the above-mentioned rhenium-poor slag, put it into a muffle furnace, and pass air for oxidative roasting at 270 ° C for 7.0 h, and open the tail gas absorption and condensation device at the same time; In percentage terms, it contains 1.36% rhenium, 0.59% arsenic, 23.32% copper, 42.02% bismuth, and 0.88% sulfur;
[0034] b. Take the rhenium-rich slag in step a and carry out selective leaching under oxygen pressure, the leaching process is two-stage countercurrent leaching, and the leaching conditions are the same, wherein the leaching solvent is hydrogen peroxide, and the solid-liquid mass volume ratio is 5:1, and saturated sodium carbonate is used before leaching The pH value of the solution was adj...
PUM
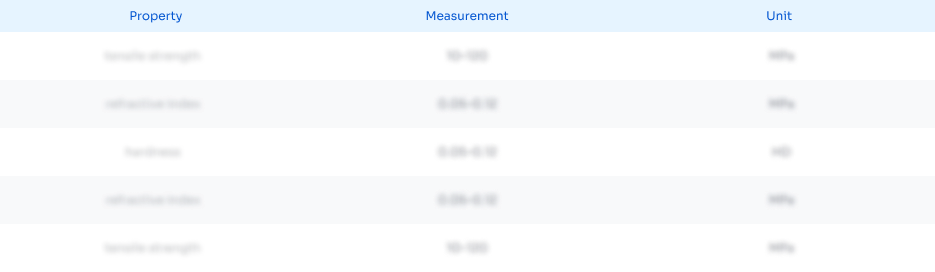
Abstract
Description
Claims
Application Information

- Generate Ideas
- Intellectual Property
- Life Sciences
- Materials
- Tech Scout
- Unparalleled Data Quality
- Higher Quality Content
- 60% Fewer Hallucinations
Browse by: Latest US Patents, China's latest patents, Technical Efficacy Thesaurus, Application Domain, Technology Topic, Popular Technical Reports.
© 2025 PatSnap. All rights reserved.Legal|Privacy policy|Modern Slavery Act Transparency Statement|Sitemap|About US| Contact US: help@patsnap.com