Method for preparing high-grade secondary zinc oxide in rotary kiln through oxygen enriched combustion
A technology of oxygen-enriched combustion and sub-zinc oxide, applied in rotary drum furnaces, furnaces, furnace types, etc., can solve the problems of difficult to control kiln conditions, large temperature changes, low recovery rate, etc., to reduce energy consumption and production costs, The effect of improving combustion efficiency and increasing throughput
- Summary
- Abstract
- Description
- Claims
- Application Information
AI Technical Summary
Problems solved by technology
Method used
Examples
example 1
[0016] Example 1. A variety of complex low-zinc materials are mixed with coke powder (5800 kcal) and then added to a Ф3.2*50m rotary kiln to produce secondary zinc oxide powder. The composition of each material is shown in Table 1:
[0017] Table 1 Composition of zinc-containing materials (raw materials) (%)
[0018] name
[0019] Note: The unit of indium (In) content in the table is g / t, the same below.
[0020] Each material is mixed with coke powder, and the coke powder accounts for 31% by mass of the mixture. The mixture added per hour is 13.8 tons, and the Roots blower is used to feed 4800Nm during the combustion process. 3 / h, the oxygen-enriched air with an oxygen content of 26.3%, the temperature in the kiln is 1240°C, and the negative pressure in the kiln is 45Pa. The components of the produced boiler powder, bag powder and kiln slag are shown in Table 2:
[0021] Table 2 Zinc-containing material (product) composition (%)
[0022] name
[0023]...
example 2
[0027] Example 2. A variety of complex low-zinc materials are mixed with coke powder (5700 kcal) and then added to a Ф2.5*38m rotary kiln to produce secondary zinc oxide powder. The composition of each material is shown in Table 4:
[0028] Table 4 Composition of zinc-containing materials (raw materials) (%)
[0029] name
Zn
Pb
In
Fe
S
Ag
Ca
Cl
Gas Ash
8.24
0.91
145
22.72
1.87
13
2.88
2.57
Neutralize iron slag
11.2
/
115
10.3
16.0
/
18.2
/
zinc lead slag
5.84
1.92
165
27.01
5.27
41
8.7
/
oxide ore
23.24
5.59
31
10.74
0.34
84
4.26
/
Back to powder
20.53
4.08
228
12.44
2.91
20
2.51
2.52
[0030] Each material is mixed with coke powder, and the coke powder accounts for 34% by mass of the mixture. The mixture added per hour is 7.2 tons, and the Roots blower is used to feed 3800Nm duri...
PUM
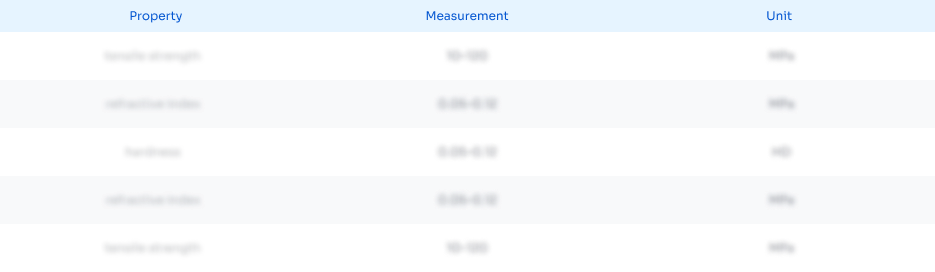
Abstract
Description
Claims
Application Information

- R&D Engineer
- R&D Manager
- IP Professional
- Industry Leading Data Capabilities
- Powerful AI technology
- Patent DNA Extraction
Browse by: Latest US Patents, China's latest patents, Technical Efficacy Thesaurus, Application Domain, Technology Topic, Popular Technical Reports.
© 2024 PatSnap. All rights reserved.Legal|Privacy policy|Modern Slavery Act Transparency Statement|Sitemap|About US| Contact US: help@patsnap.com