Manufacturing technology of dual-layer carbon fiber tube with foam interlayer
A carbon fiber tube and foam layer technology, applied in the field of carbon fiber, can solve the problems of uneven thickness of glue, high noise and vibration of truss-type vehicles, and increased weight of carbon fiber tube, so as to avoid the problem of non-axis, reduce the subsequent work, glue Evenly distributed effect
- Summary
- Abstract
- Description
- Claims
- Application Information
AI Technical Summary
Problems solved by technology
Method used
Image
Examples
Embodiment Construction
[0028] The words "upper", "lower" and "bottom" used herein are used for the convenience of explaining the structure of the present invention, and do not constitute any form of limitation to the content of the claims of the present invention.
[0029] Such as Figure 1-Figure 8 Shown is a manufacturing process of a double-layer carbon fiber tube with a foam interlayer, wherein the double-layer carbon fiber tube is sequentially provided with an outer layer carbon fiber tube 1, a foam layer 2, and an inner layer carbon fiber tube 3 from the outside to the inside; the double-layer carbon fiber tube Both ends of the carbon fiber tube are respectively connected with a metal joint 4 .
[0030] Such as Figure 7 As shown, the metal joint 4 includes a first convex platform 51, a second convex platform 61 is arranged on the upper end surface of the first convex platform 51, and a third convex platform 71 is arranged on the upper end surface of the second convex platform 61; The upper ...
PUM
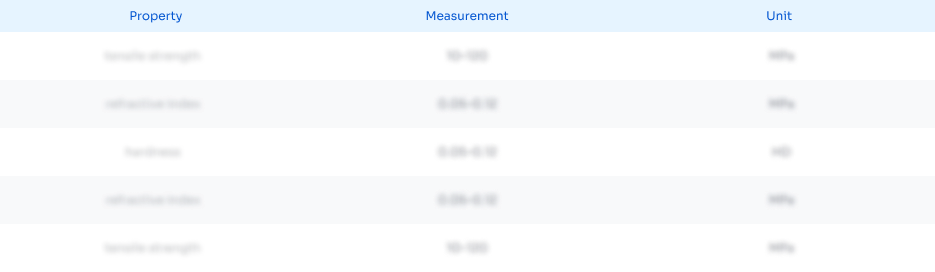
Abstract
Description
Claims
Application Information

- R&D Engineer
- R&D Manager
- IP Professional
- Industry Leading Data Capabilities
- Powerful AI technology
- Patent DNA Extraction
Browse by: Latest US Patents, China's latest patents, Technical Efficacy Thesaurus, Application Domain, Technology Topic, Popular Technical Reports.
© 2024 PatSnap. All rights reserved.Legal|Privacy policy|Modern Slavery Act Transparency Statement|Sitemap|About US| Contact US: help@patsnap.com