Graphene antibacterial brush wire as well as preparation method and application thereof
A graphene and graphene composite technology, applied in brushes, applications, bristles, etc., can solve problems such as limited antibacterial effect and toxicity, and achieve the effects of avoiding bacterial growth, lasting efficacy, and broad antibacterial spectrum.
- Summary
- Abstract
- Description
- Claims
- Application Information
AI Technical Summary
Problems solved by technology
Method used
Image
Examples
Embodiment 1
[0031] The present embodiment provides a kind of preparation method of graphene antibacterial brush filament, and its reaction mechanism is as follows figure 1 shown. Specifically include the following steps:
[0032] S1, mixing molten PA610 slices with graphene powder, extruding and granulating to prepare graphene composite slices;
[0033] S2. Dry the graphene composite slices and put them into an injection molding machine. After softening, use a push rod or a rotating screw to continuously extrude from the die, and cool to prepare the brush filaments.
[0034] In step S1, the content of graphene in the graphene composite slice is 0.3wt%.
[0035] In step S1, the mixing temperature is 220° C., the mixing speed is 10000 rad / min, and the mixing time is 20 minutes; the extrusion granulation temperature is 200-270° C.
[0036] In step S2, the drying temperature of the graphene composite slice is 100° C., and the drying time is 5 hours; the softening temperature is 200° C.; th...
Embodiment 2
[0038] The present embodiment provides a kind of preparation method of graphene antibacterial brush wire, comprises the following steps:
[0039] S1, mixing molten PA610 slices with graphene powder, extruding and granulating to prepare graphene composite slices;
[0040] S2. Dry the graphene composite slices and put them into an injection molding machine. After softening, use a push rod or a rotating screw to continuously extrude from the die, and cool to prepare the brush filaments.
[0041] In step S1, the content of graphene in the graphene composite slice is 1 wt%.
[0042] In step S1, the mixing temperature is 240° C., the mixing speed is 8000 rad / min, and the mixing time is 10 minutes; the extrusion granulation temperature is 200-270° C.
[0043] In step S2, the drying temperature of the graphene composite slice is 70° C., and the drying time is 20 hours; the softening temperature is 230° C.; the extruding temperature is 180-250° C.
Embodiment 3
[0045] The present embodiment provides a kind of preparation method of graphene antibacterial brush wire, comprises the following steps:
[0046] S1, mixing molten PA610 slices with graphene powder, extruding and granulating to prepare graphene composite slices;
[0047] S2. Dry the graphene composite slices and put them into an injection molding machine. After softening, use a push rod or a rotating screw to continuously extrude from the die, and cool to prepare the brush filaments.
[0048] In step S1, the content of graphene in the graphene composite slice is 0.5wt%.
[0049] In step S1, the mixing temperature is 250° C., the mixing speed is 5000 rad / min, and the mixing time is 40 minutes; the extrusion granulation temperature is 200-270° C.
[0050]In step S2, the drying temperature of the graphene composite slice is 80° C., and the drying time is 15 hours; the softening temperature is 220° C.; the extruding temperature is 180-250° C.
PUM
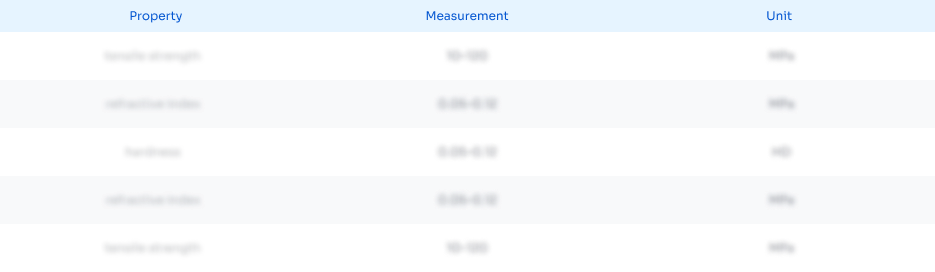
Abstract
Description
Claims
Application Information

- R&D
- Intellectual Property
- Life Sciences
- Materials
- Tech Scout
- Unparalleled Data Quality
- Higher Quality Content
- 60% Fewer Hallucinations
Browse by: Latest US Patents, China's latest patents, Technical Efficacy Thesaurus, Application Domain, Technology Topic, Popular Technical Reports.
© 2025 PatSnap. All rights reserved.Legal|Privacy policy|Modern Slavery Act Transparency Statement|Sitemap|About US| Contact US: help@patsnap.com