Traction spherical hinge for rail vehicles and rigidity design method of traction spherical hinge
A rail vehicle and stiffness design technology, applied in the direction of springs, devices that move laterally between the chassis and the bogie, can solve problems such as short fatigue life, wrinkle cracking, and inability to meet nonlinear stiffness requirements, and achieve improved resistance. Fatigue performance, rubber swelling reduction effect
- Summary
- Abstract
- Description
- Claims
- Application Information
AI Technical Summary
Problems solved by technology
Method used
Image
Examples
Embodiment Construction
[0028] Attached below Figures 1 to 3 Embodiments of the present invention are described in detail.
[0029] A traction ball joint for rail vehicles, comprising a casing 1, a mandrel 2, and a rubber layer 3 vulcanized and bonded between the mandrel 2 and the casing 1, and is characterized in that the middle of the bonding part between the mandrel 2 and the rubber layer 3 is The segment is an arc surface protrusion 21 protruding radially outward, the center line of the arc surface protrusion 21 coincides with the center line of the mandrel 1, and the deformed surface 31 of the rubber layer 3 is axially outward The inner surface gradually approaches the outer convex arc surface of the inner wall of the jacket 1, the arc radius of the deformed surface 31 is R1, and the arc radius of the arc surface protrusion 21 is R2, R1<R2.
[0030] As shown in the figure, the mandrel 2 has an arc-shaped protrusion 21, and the deformed surface of the rubber layer 3 is an outwardly convex arc-s...
PUM
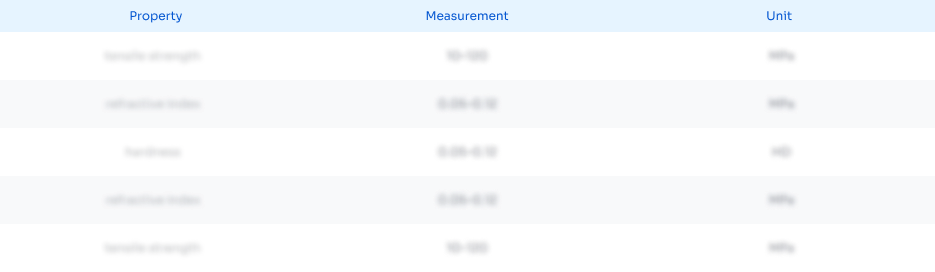
Abstract
Description
Claims
Application Information

- R&D Engineer
- R&D Manager
- IP Professional
- Industry Leading Data Capabilities
- Powerful AI technology
- Patent DNA Extraction
Browse by: Latest US Patents, China's latest patents, Technical Efficacy Thesaurus, Application Domain, Technology Topic, Popular Technical Reports.
© 2024 PatSnap. All rights reserved.Legal|Privacy policy|Modern Slavery Act Transparency Statement|Sitemap|About US| Contact US: help@patsnap.com