Energy-saving processing equipment used in early-stage production of non-woven cloth
A processing equipment and non-weft fabric technology, which is applied in the textile field, can solve the problems of cloth and film damage, low tearing efficiency, and unstable tearing process, so as to achieve improved effect, stable tearing process, and efficient tearing method. Effect
- Summary
- Abstract
- Description
- Claims
- Application Information
AI Technical Summary
Problems solved by technology
Method used
Image
Examples
Embodiment 1
[0030] figure 1 It is a schematic diagram of the structure of the unidirectional fabric tearing film equipment for non-weft fabrics, figure 2 It is a schematic diagram of the front view of the unidirectional fabric tearing film equipment for non-weft fabrics, image 3 Schematic diagram of the suction device, Figure 4 It is a schematic diagram of the structure of the cloth pulling mechanism, Figure 5 is a schematic diagram of the structure of the roller, Figure 6 A cross-sectional schematic diagram of the roller. Such as figure 1 , figure 2 , image 3 , Figure 4 , Figure 5 and Figure 6 As shown, an energy-saving non-weft cloth production pre-processing equipment includes a heating part 1, and the heating part 1 is used to heat the cloth with film to soften the glue between the cloth 10 and the isolation film 20; the cloth film is separated Part 2, the cloth-film separation part 2 is arranged at the rear end of the heating part 1, the cloth-film separation part...
Embodiment 2
[0042] Such as figure 1 , figure 2 , image 3 , Figure 4 , Figure 5 and Figure 6 As shown, the components that are the same as or corresponding to those in the first embodiment are marked with the corresponding reference numerals in the first embodiment. For the sake of simplicity, only the differences from the first embodiment will be described below. The difference between the second embodiment and the first embodiment is that a baffle 3 is also provided inside the roller 2112, and the baffle 3 is fixed on the fixed shaft 2111 through a connecting piece 31, and the baffle 3 is used for Block the adsorption hole 2115 on the roller 2112 when it rotates to the baffle 3;
[0043] The setting of the baffle 3 makes the isolation film 20 move to the position of the baffle 3 with the roller 2112, because the baffle 3 blocks the adsorption hole 2115 on the roller 2112 in this area, so that when the isolation film 20 is transported to this area , the roller 2112 no longer has ...
PUM
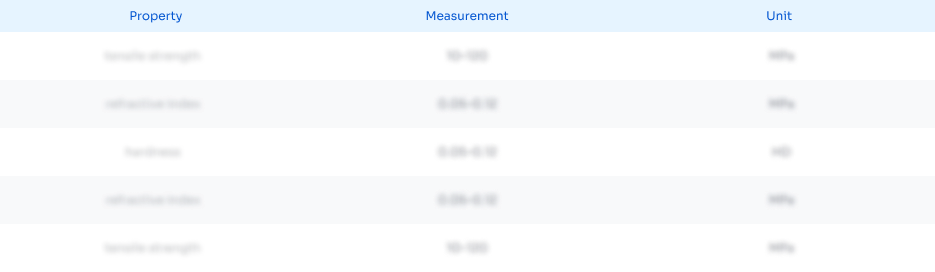
Abstract
Description
Claims
Application Information

- R&D Engineer
- R&D Manager
- IP Professional
- Industry Leading Data Capabilities
- Powerful AI technology
- Patent DNA Extraction
Browse by: Latest US Patents, China's latest patents, Technical Efficacy Thesaurus, Application Domain, Technology Topic, Popular Technical Reports.
© 2024 PatSnap. All rights reserved.Legal|Privacy policy|Modern Slavery Act Transparency Statement|Sitemap|About US| Contact US: help@patsnap.com