Manufacturing method of flip-flop lace
A manufacturing method and technology for flip-flops, which are applied in the field of slippers, can solve the problems of affecting the appearance of flip-flops, no bumpy feeling, poor 3D effect, etc., and achieve the effects of strong bumpy feeling, easy operation and simple process.
- Summary
- Abstract
- Description
- Claims
- Application Information
AI Technical Summary
Problems solved by technology
Method used
Image
Examples
Embodiment 1
[0024] A kind of manufacturing method of flip-flop strap of the present embodiment, comprises the following steps:
[0025] Glue dispensing: Put the lower mold of the flip-flop strap into the glue dispenser, and use the glue dispenser to dispense glue into the cavity of the lower mold of the flip-flop strap to form a preset pattern;
[0026] Thermoforming: Put the lower mold of the flip-flop strap into the drying equipment for heating and forming to solidify the pattern;
[0027] Injection molding: Put the lower mold of the flip-flop strap into the injection molding machine, close the upper mold of the flip-flop strap, make the cavity of the upper mold of the flip-flop strap match the cavity of the lower mold of the flip-flop strap, through injection molding The machine injects plastic into the cavity of the upper mold of the flip-flop strap and the cavity of the lower mold of the flip-flop strap, and the plastic is formed on the upper surface of the cured pattern;
[0028] M...
Embodiment 2
[0041] A kind of manufacturing method of flip-flop strap of the present embodiment, comprises the following steps:
[0042] Glue dispensing: Put the lower mold of the flip-flop strap into the glue dispenser, and use the glue dispenser to dispense glue into the cavity of the lower mold of the flip-flop strap to form a preset pattern;
[0043] Thermoforming: Put the lower mold of the flip-flop strap into the drying equipment for heating and forming to solidify the pattern;
[0044] Injection molding: Put the lower mold of the flip-flop strap into the injection molding machine, close the upper mold of the flip-flop strap, make the cavity of the upper mold of the flip-flop strap match the cavity of the lower mold of the flip-flop strap, through injection molding The machine injects plastic into the cavity of the upper mold of the flip-flop strap and the cavity of the lower mold of the flip-flop strap, and the plastic is formed on the upper surface of the cured pattern;
[0045] M...
Embodiment 3
[0059] A kind of manufacturing method of flip-flop strap of the present embodiment, comprises the following steps:
[0060] Glue dispensing: Put the lower mold of the flip-flop strap into the glue dispenser, and use the glue dispenser to dispense glue into the cavity of the lower mold of the flip-flop strap to form a preset pattern;
[0061] Thermoforming: Put the lower mold of the flip-flop strap into the drying equipment for heating and forming to solidify the pattern;
[0062] Injection molding: Put the lower mold of the flip-flop strap into the injection molding machine, close the upper mold of the flip-flop strap, make the cavity of the upper mold of the flip-flop strap match the cavity of the lower mold of the flip-flop strap, through injection molding The machine injects plastic into the cavity of the upper mold of the flip-flop strap and the cavity of the lower mold of the flip-flop strap, and the plastic is formed on the upper surface of the cured pattern;
[0063] M...
PUM
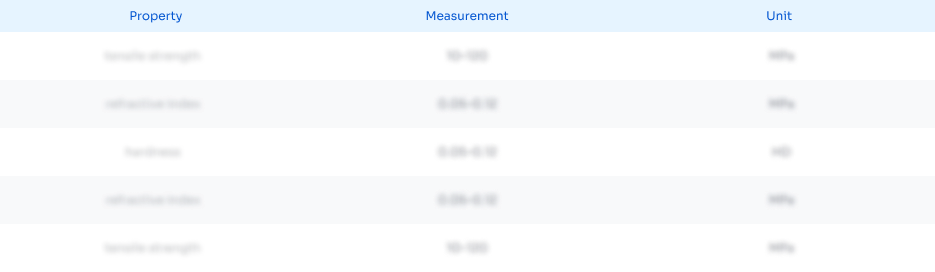
Abstract
Description
Claims
Application Information

- Generate Ideas
- Intellectual Property
- Life Sciences
- Materials
- Tech Scout
- Unparalleled Data Quality
- Higher Quality Content
- 60% Fewer Hallucinations
Browse by: Latest US Patents, China's latest patents, Technical Efficacy Thesaurus, Application Domain, Technology Topic, Popular Technical Reports.
© 2025 PatSnap. All rights reserved.Legal|Privacy policy|Modern Slavery Act Transparency Statement|Sitemap|About US| Contact US: help@patsnap.com