Extraction method adopting deep-hole presplitting blasting along seam floor for coal roadway driving
A technology of coal seam floor and pre-splitting blasting, which is applied in mining fluid, mining equipment, earthwork drilling and mining, etc. It can solve the problems of waste of drilling holes, small extraction radius, and long extraction cycle, and achieve high efficiency, construction safety, and Effect of preventing coal and gas outburst
- Summary
- Abstract
- Description
- Claims
- Application Information
AI Technical Summary
Problems solved by technology
Method used
Image
Examples
Embodiment 1
[0025] A coal roadway excavation method along the deep hole pre-splitting blasting of the coal seam floor, the steps are as follows:
[0026] 1. Before the coal mining roadway (1) is excavated, the gas drainage holes (3) are constructed along the front of the coal mining roadway (1) 40m, and the gas drainage holes (3) are constructed within the range of 20m each, and each gas drainage hole is constructed. Immediately lower the drainage pipe to plug and drain the gas according to the conventional method, and the distance between the final holes of the gas drainage holes (3) is 5m;
[0027] 2. Construct a 5m long, 3.7m wide, and 1.4m deep floor drilling field (4) directly below the head of the coal roadway (1) to be excavated, and construct 3 parallel to the coal seam (2) in the floor drilling field (4). blast hole (5), the blast hole (5) is 0.5m away from the floor of the roadway to be excavated (1), and the first blast hole is drilled in the same direction as the roadway to be...
Embodiment 2
[0032] A coal roadway excavation method along the deep hole pre-splitting blasting of the coal seam floor, the steps are as follows:
[0033] 1. Before the coal mining roadway (1) is excavated, the gas drainage holes (3) are constructed along the front of the coal mining roadway (1) 50m, and the gas drainage holes (3) are constructed within the range of 20m each, and each gas drainage hole is constructed. Immediately lower the drainage pipe to plug and drain the gas according to the conventional method, and the distance between the final holes of the gas drainage holes (3) is 5.5m;
[0034] 2. Construct a floor drilling field (4) with a length of 6m, a width of 3.2m, and a depth of 1.6m directly below the head of the coal roadway (1) to be excavated, and construct three parallel to the coal seam (2) in the floor drilling field (4). blast hole (5), the blast hole (5) is 0.7m away from the bottom plate of the coal roadway (1) to be excavated, and the drilling direction of the fi...
Embodiment 3
[0039] A coal roadway excavation method along the deep hole pre-splitting blasting of the coal seam floor, the steps are as follows:
[0040] 1. Before the coal mining roadway (1) is excavated, the gas drainage holes (3) are constructed along the front of the coal mining roadway (1) 60m, and the gas drainage holes (3) are constructed within the range of 20m each, and each gas drainage hole is constructed. Immediately lower the drainage pipe to plug and drain the gas according to the conventional method, and the distance between the final holes of the gas drainage holes (3) is 6m;
[0041]2. Construction is 5.3m long, 4m wide, and 2m deep floor drilling site (4) directly below the head of the coal roadway (1) to be excavated. In the floor drilling site (4), 3 parallel mines are constructed in the floor drilling site (4). The blast hole (5), the distance between the blast hole (5) and the bottom plate of the coal roadway (1) to be excavated is 1.2m, and the drilling direction of...
PUM
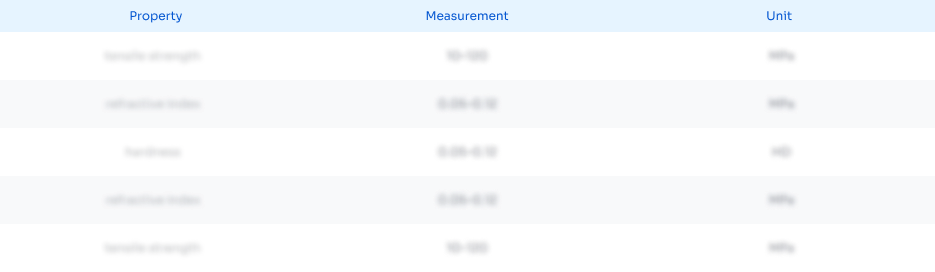
Abstract
Description
Claims
Application Information

- R&D
- Intellectual Property
- Life Sciences
- Materials
- Tech Scout
- Unparalleled Data Quality
- Higher Quality Content
- 60% Fewer Hallucinations
Browse by: Latest US Patents, China's latest patents, Technical Efficacy Thesaurus, Application Domain, Technology Topic, Popular Technical Reports.
© 2025 PatSnap. All rights reserved.Legal|Privacy policy|Modern Slavery Act Transparency Statement|Sitemap|About US| Contact US: help@patsnap.com