Pre-treatment technique for punch-formed metal product
A metal product and stamping forming technology, applied in the direction of pretreatment surface, cleaning method using liquid, device for coating liquid on the surface, etc., can solve the problems affecting the surface quality of parts, prolonging the production cycle, reducing work efficiency, etc., to achieve Effects of prolonging service life, improving performance, and improving work efficiency
- Summary
- Abstract
- Description
- Claims
- Application Information
AI Technical Summary
Problems solved by technology
Method used
Examples
Embodiment 1
[0024] A pretreatment process for stamped and formed metal products, comprising the following steps:
[0025] 1. Clean the surface of the metal product, and then bake it at 120°C for 10 minutes, then cool it down to room temperature;
[0026] 2. Coat the surface of the metal product treated in step 1 with an oxide film, add a stabilizer to the oxide film at the same time, and then conduct conductive oxidation treatment;
[0027] 3. Spread the anti-wear agent evenly on the surface of the metal product treated in step 2, and then put it into the oven at 100°C for 60 minutes;
[0028] 4. Immerse the metal product processed in step 3 into the anti-wear agent while it is hot, take it out and let it dry naturally, then coat the surface of the metal product with an insulating layer, and finally perform laser gasification treatment.
[0029] Step 1 Cleaning of metal products uses high-pressure water to spray onto the surface of metal products to remove the dirt attached to the surfac...
Embodiment 2
[0037] A pretreatment process for stamped and formed metal products, comprising the following steps:
[0038] 1. Clean the surface of the metal product, and then bake it at 100°C for 10 minutes, then cool it down to room temperature;
[0039] 2. Coat the surface of the metal product treated in step 1 with an oxide film, add a stabilizer to the oxide film at the same time, and then conduct conductive oxidation treatment;
[0040] 3. Apply the anti-wear agent evenly on the surface of the metal product treated in step 2, and then put it into the oven at 80°C for 60 minutes;
[0041] 4. Immerse the metal product processed in step 3 into the anti-wear agent while it is hot, take it out and let it dry naturally, then coat the surface of the metal product with an insulating layer, and finally perform laser gasification treatment.
[0042] Step 1 Cleaning of metal products uses high-pressure water to spray onto the surface of metal products to remove the dirt attached to the surface....
Embodiment 3
[0050] A pretreatment process for stamped and formed metal products, comprising the following steps:
[0051] 1. Clean the surface of the metal product, and then bake it at 120°C for 10 minutes, then cool it down to room temperature;
[0052] 2. Coat the surface of the metal product treated in step 1 with an oxide film, add a stabilizer to the oxide film at the same time, and then conduct conductive oxidation treatment;
[0053] 3. Spread the anti-wear agent evenly on the surface of the metal product treated in step 2, and then put it into an oven at 80°C for 80 minutes;
[0054] 4. Immerse the metal product processed in step 3 into the anti-wear agent while it is hot, take it out and let it dry naturally, then coat the surface of the metal product with an insulating layer, and finally perform laser gasification treatment.
[0055] Step 1 Cleaning of metal products uses high-pressure water to spray onto the surface of metal products to remove the dirt attached to the surface....
PUM
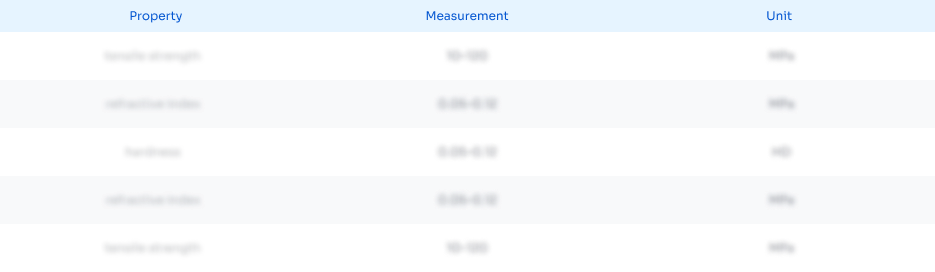
Abstract
Description
Claims
Application Information

- R&D Engineer
- R&D Manager
- IP Professional
- Industry Leading Data Capabilities
- Powerful AI technology
- Patent DNA Extraction
Browse by: Latest US Patents, China's latest patents, Technical Efficacy Thesaurus, Application Domain, Technology Topic, Popular Technical Reports.
© 2024 PatSnap. All rights reserved.Legal|Privacy policy|Modern Slavery Act Transparency Statement|Sitemap|About US| Contact US: help@patsnap.com