Storage logistic robot group control system based on visual guidance and RFID navigation
A technology of warehousing logistics and robot groups, which is applied in control/adjustment systems, two-dimensional position/channel control, instruments, etc., and can solve problems such as high prices, high requirements for site laying, and positioning switches that are easily blocked by shelves.
- Summary
- Abstract
- Description
- Claims
- Application Information
AI Technical Summary
Problems solved by technology
Method used
Image
Examples
Embodiment Construction
[0065] The present invention will be further described in detail below in conjunction with the accompanying drawings.
[0066] Such as figure 1 As shown, the AGV transport vehicle in this design communicates with the computer through a router, which can satisfy the need for one computer to control the operation of multiple AGVs at the same time. The route planned by the computer is sent to the specified numbered car through WIFI. During the operation, the AGV reports the current status and geographical location coordinates of the car through WIFI in real time, and keeps walking with the host computer in real time, and performs real-time path planning one by one.
[0067] Such as figure 2 As shown, the hardware block diagram of this design includes master CPU, slave CPU, WiFi module ATK-RM04, motor driver module BLDC, camera module OC5647, gyroscope module MPU6050, infrared switch tube E18-D80NK, electric actuator XTL100 and radio frequency identification module rc522.
[0...
PUM
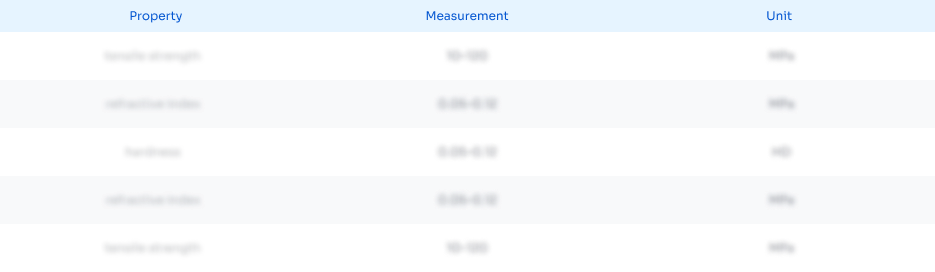
Abstract
Description
Claims
Application Information

- R&D
- Intellectual Property
- Life Sciences
- Materials
- Tech Scout
- Unparalleled Data Quality
- Higher Quality Content
- 60% Fewer Hallucinations
Browse by: Latest US Patents, China's latest patents, Technical Efficacy Thesaurus, Application Domain, Technology Topic, Popular Technical Reports.
© 2025 PatSnap. All rights reserved.Legal|Privacy policy|Modern Slavery Act Transparency Statement|Sitemap|About US| Contact US: help@patsnap.com