Energy-saving environmentally-friendly de-waxing kiln and de-waxing process
A kiln and process technology, applied in the field of tunnel kiln, can solve the problem of high burst rate of products, and achieve the effects of low transformation cost, simple overall structure and production cost saving.
- Summary
- Abstract
- Description
- Claims
- Application Information
AI Technical Summary
Problems solved by technology
Method used
Image
Examples
Embodiment 1
[0024] Embodiment 1: as figure 1 As shown, the wax removal kiln of this embodiment includes the connected first tunnel kiln 1 and the second tunnel kiln 3, and the product is preheated to 180°C to 300°C through the second tunnel kiln 3 and kept warm for a certain period of time before being pushed into the first tunnel kiln 1. By adding the second tunnel kiln 3, it can ensure that the product has sufficient heat preservation time, so as to avoid subsequent product waxing and bursting. Wherein, the preheating temperature range is any temperature value between 180°C and 300°C, such as 180°C, 181°C, 182°C, 183°C...298°C, 299°C, 300°C, etc.
Embodiment 2
[0025] Embodiment 2: as figure 1 As shown, one end of the first tunnel kiln 1 is the product input end and is provided with the first propeller 2, and the other end of the first tunnel kiln 1 is the product output end; also includes the second tunnel kiln 3, the second tunnel kiln 3 The product output end communicates with the product input end of the first tunnel kiln 1 , and the second propeller 6 is installed at the product input end of the second tunnel kiln 3 . The heat preservation temperature of the product in the second tunnel kiln 3 remains basically the same as the temperature of the low-temperature section of the first tunnel kiln 1, and an independent heater can be used for heating and heat preservation. The channel is communicated with the furnace bottom channel of the low temperature section 10 of the first tunnel kiln 1 through the induced air channel 4, and the furnace bottom hot air flow of the first tunnel kiln 1 is introduced to the furnace bottom of the sec...
PUM
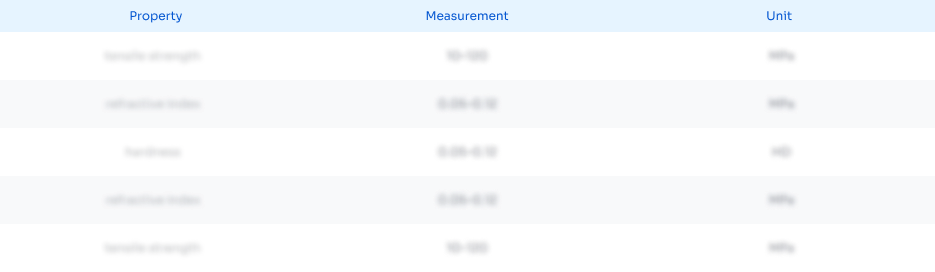
Abstract
Description
Claims
Application Information

- R&D Engineer
- R&D Manager
- IP Professional
- Industry Leading Data Capabilities
- Powerful AI technology
- Patent DNA Extraction
Browse by: Latest US Patents, China's latest patents, Technical Efficacy Thesaurus, Application Domain, Technology Topic, Popular Technical Reports.
© 2024 PatSnap. All rights reserved.Legal|Privacy policy|Modern Slavery Act Transparency Statement|Sitemap|About US| Contact US: help@patsnap.com