Wood drying method
A drying method and technology for wood, which are used in wood drying, preliminary treatment to promote the drying of solid materials, drying of solid materials, etc., can solve the problems of long drying cycle, time-consuming and energy-consuming, shortening drying time, etc. , Improve drying speed and reduce drying defects
- Summary
- Abstract
- Description
- Claims
- Application Information
AI Technical Summary
Problems solved by technology
Method used
Examples
Embodiment 1
[0030] A method for drying wood, comprising the following specific steps:
[0031]Step 1. Steam explosion treatment: The high-pressure blasting device includes a pressure tank, a steam generator and a pressurized pump. Put the wood that has been sawn into a board into the pressure tank, feed saturated steam, heat it to 60°C, keep it warm for 1 hour, and then use The booster pump pressurizes the pressure tank. After pressurizing to 0.5MPa, quickly open the pressure relief valve on the pressure tank and repeat the above steps 3 times;
[0032] Step 2. Impregnation treatment: put the plate after steam explosion treatment into a sealed tank, vacuum the tank to 0.08MPa negative pressure state, and keep it for 10 minutes. Under this negative pressure state, triethylamine trihydrofluoride and The mixed solution of ammonium hexafluorophosphate is filled with sealed tank, and the mass ratio of triethylamine trihydrofluoride and ammonium hexafluorophosphate in the mixed solution of desc...
Embodiment 2
[0038] A method for drying wood, comprising the following specific steps:
[0039] Step 1. Steam explosion treatment: The high-pressure blasting device includes a pressure tank, a steam generator and a pressurized pump. Put the wood that has been sawn into a board into the pressure tank, feed saturated steam, heat it to 80°C, keep it warm for 2 hours, and then use The booster pump pressurizes the pressure tank. After pressurizing to 1.5MPa, quickly open the pressure relief valve on the pressure tank and repeat the above steps 4 times;
[0040] Step 2. Impregnation treatment: put the plate after steam explosion treatment into a sealed tank, vacuum the tank to a negative pressure of 0.09MPa, and keep it for 20 minutes. Under this negative pressure, triethylamine trihydrofluoride and The mixed solution of ammonium hexafluorophosphate fills the sealed tank, and the mass ratio of triethylamine trihydrofluoride and ammonium hexafluorophosphate in the mixed solution of triethylamine ...
Embodiment 3
[0046] A method for drying wood, comprising the following specific steps:
[0047] Step 1. Steam explosion treatment: The high-pressure blasting device includes a pressure tank, a steam generator and a pressurized pump. Put the wood that has been sawn into a board into the pressure tank, feed saturated steam, heat it to 90°C, keep it warm for 3 hours, and then use The booster pump pressurizes the pressure tank. After pressurizing to 2MPa, quickly open the pressure relief valve on the pressure tank and repeat the above steps 5 times;
[0048] Step 2. Impregnation treatment: put the plate after steam explosion treatment into a sealed tank, vacuum the tank to 0.1MPa negative pressure state, and keep it for 30 minutes. Under this negative pressure state, triethylamine trihydrofluoride and The mixed solution of ammonium hexafluorophosphate fills the sealed tank, and the mass ratio of triethylamine trihydrofluoride and ammonium hexafluorophosphate in the mixed solution of triethylam...
PUM
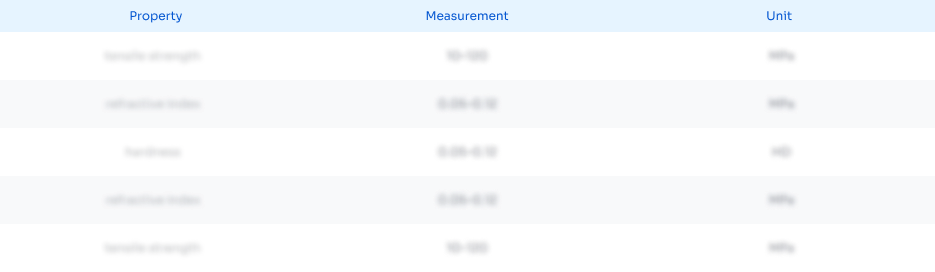
Abstract
Description
Claims
Application Information

- Generate Ideas
- Intellectual Property
- Life Sciences
- Materials
- Tech Scout
- Unparalleled Data Quality
- Higher Quality Content
- 60% Fewer Hallucinations
Browse by: Latest US Patents, China's latest patents, Technical Efficacy Thesaurus, Application Domain, Technology Topic, Popular Technical Reports.
© 2025 PatSnap. All rights reserved.Legal|Privacy policy|Modern Slavery Act Transparency Statement|Sitemap|About US| Contact US: help@patsnap.com