High thermal conductivity carbon fiber cloth and preparation method thereof
A carbon fiber cloth, high thermal conductivity technology, applied in the preparation of high thermal conductivity carbon fiber cloth, the field of high thermal conductivity carbon fiber cloth, can solve the problems of low heat dissipation, poor reliability, increase the thermal conductivity of carbon fiber bundles, etc., to improve thermal conductivity, increase heat Conductivity, the effect of excellent performance
- Summary
- Abstract
- Description
- Claims
- Application Information
AI Technical Summary
Problems solved by technology
Method used
Examples
preparation example Construction
[0031] The invention also proposes a preparation method of the high thermal conductivity carbon fiber cloth.
[0032] (1) Stir and mix 20-50 parts of micro-nano ceramic powder and 30-60 parts of binder resin evenly, and the stirring time is 30min-2h to obtain a mixture;
[0033] (2) Add 10-40 parts of curing agent to the mixture, stir and mix for 30min-5h to obtain high thermal conductivity carbon fiber bonding resin;
[0034] (3) Coat the high thermal conductivity carbon fiber adhesive resin on the carbon fiber cloth with an impregnation machine, the coating thickness is 30-500um, the coating heating temperature is 40-75 degrees, the coating time is 10-100min, and the normal temperature is cooled for more than 2h , to obtain coated carbon fiber cloth;
[0035] (4) Make the hot roller press carry out 3-stage heating and pressing to the coated carbon fiber cloth, the first heating and pressing temperature is 60-100°C, and the time is 0.5h-3h; the second heating and pressing te...
Embodiment 1
[0039] 1. Carbon fiber cloth adopts carbon fiber woven cloth;
[0040] 2. Get 18KG micro-nano ceramic powder, wherein the micro-nano ceramic powder contains 92% by weight of silicon carbide SiC and 8% by weight of graphite;
[0041] 3. Take 30KG of epoxy resin and 8KG of trimethylhexamethylenediamine (TMD);
[0042] 4. First remove the water from the obtained micro-nano ceramic powder, then add the obtained epoxy resin into the mixer, and stir for 1 hour to obtain a mixture;
[0043] 5. Take 8KG of trimethylhexamethylenediamine (TMD) and add it to the mixture, and continue stirring and mixing for 1 hour to obtain a high thermal conductivity carbon fiber adhesive resin;
[0044]6. Use an impregnation machine to coat the high thermal conductivity carbon fiber adhesive resin on the carbon fiber cloth, coat the thickness of 40um at a heating temperature of 55 degrees, and then cool it at normal temperature for 2 hours to obtain the coated carbon fiber cloth;
[0045] 7. Use a ho...
Embodiment 2
[0048] 1. Carbon fiber cloth adopts carbon fiber woven cloth
[0049] 2. Take 12KG micro-nano ceramic powder, wherein the micro-nano ceramic powder contains silicon carbide SiC with a weight percentage of 100%
[0050] 3. Take 30KG of epoxy resin and 8KG of trimethylhexamethylenediamine (TMD)
[0051] 4. First remove the water from the obtained micro-nano ceramic powder, then add the obtained epoxy resin into the mixer, and stir for 1 hour to obtain a mixture;
[0052] 5. Add 8KG of trimethylhexamethylenediamine (TMD) into the mixture, and continue stirring and mixing for 1 hour to obtain a high thermal conductivity carbon fiber adhesive resin. Coat carbon fiber with high thermal conductivity carbon fiber bonding resin using impregnator
[0053] 6. On the cloth, coat it with a thickness of 40um at a heating temperature of 55 degrees, and then cool it at normal temperature for 2 hours to obtain a coated carbon fiber cloth;
[0054] 7. Use a hot roller press to heat and press...
PUM
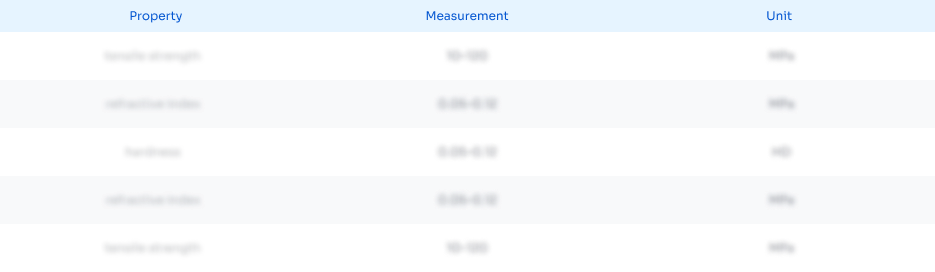
Abstract
Description
Claims
Application Information

- R&D
- Intellectual Property
- Life Sciences
- Materials
- Tech Scout
- Unparalleled Data Quality
- Higher Quality Content
- 60% Fewer Hallucinations
Browse by: Latest US Patents, China's latest patents, Technical Efficacy Thesaurus, Application Domain, Technology Topic, Popular Technical Reports.
© 2025 PatSnap. All rights reserved.Legal|Privacy policy|Modern Slavery Act Transparency Statement|Sitemap|About US| Contact US: help@patsnap.com