Injection-molded part forming method requiring two stages of core pulling
A molding method and injection molding technology, applied in the field of injection molds, can solve the problems of easy interference and complex mold structure, and achieve the effect of convenient connection and reliable core pulling steps.
- Summary
- Abstract
- Description
- Claims
- Application Information
AI Technical Summary
Problems solved by technology
Method used
Image
Examples
Embodiment Construction
[0036] The present invention will be further described below in conjunction with the accompanying drawings and specific embodiments.
[0037] The injection molded part molding method of the present invention is suitable for products that simultaneously have side hole slots that require side core pulling in a side shape that requires side core pulling, and the core pulling direction of the side shape and the pulling direction of the side hole slots The core direction is inconsistent, that is, the large slider used to form the lateral shape and the core or small slider used to form the lateral hole slot need to be cored in different directions, and the lateral hole needs to be formed first. The core of the groove or the small slider is separated from the product before the large slider is cored, so as to avoid contact with the core or small slider still remaining in the side hole groove of the product when the large slider is cored. Blocks interfere with each other.
[0038] Su...
PUM
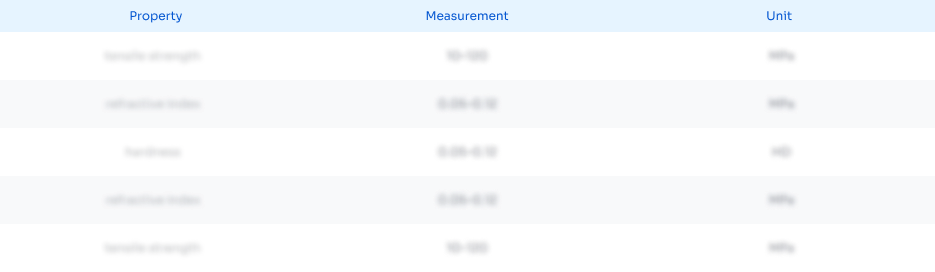
Abstract
Description
Claims
Application Information

- R&D Engineer
- R&D Manager
- IP Professional
- Industry Leading Data Capabilities
- Powerful AI technology
- Patent DNA Extraction
Browse by: Latest US Patents, China's latest patents, Technical Efficacy Thesaurus, Application Domain, Technology Topic, Popular Technical Reports.
© 2024 PatSnap. All rights reserved.Legal|Privacy policy|Modern Slavery Act Transparency Statement|Sitemap|About US| Contact US: help@patsnap.com