Simple and convenient thin metal sheet drilling machine device
A metal plate and hole processing technology, which is applied to metal processing equipment, feeding devices, positioning devices, etc., can solve the problems of high price, slow drilling speed, low drilling quality, etc., and achieves low manufacturing cost and maintenance cost. Fast punching speed and good punching quality
- Summary
- Abstract
- Description
- Claims
- Application Information
AI Technical Summary
Problems solved by technology
Method used
Image
Examples
Embodiment Construction
[0024] Such as Figure 1-Figure 6 As shown, a simple thin metal plate punching processing device of the present invention includes a body 1, an operation groove 6 is arranged in the right end surface of the body 1, and an operation groove 6 is arranged in the left side of the body 1 of the operation groove 6. A switching chamber 7 is provided, the upper and lower inner walls of the switching chamber 7 are respectively provided with a first inner spline shaft 71 and a second inner spline shaft 72, and the left inner wall of the switching chamber 7 is provided with a first sliding groove 74 , the inner bottom wall of the first sliding groove 74 is provided with a sinking groove 75, and a first guide rod 76 is arranged between the inner bottom wall of the sinking groove 75 and the inner top wall of the first sliding groove 74. A first sliding block 741 extending to the right is connected to the guide rod 76 by sliding fit. The outer surface of the first guide rod 76 at the bottom...
PUM
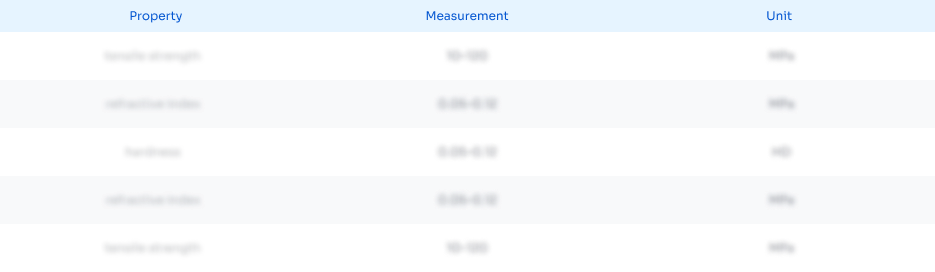
Abstract
Description
Claims
Application Information

- R&D
- Intellectual Property
- Life Sciences
- Materials
- Tech Scout
- Unparalleled Data Quality
- Higher Quality Content
- 60% Fewer Hallucinations
Browse by: Latest US Patents, China's latest patents, Technical Efficacy Thesaurus, Application Domain, Technology Topic, Popular Technical Reports.
© 2025 PatSnap. All rights reserved.Legal|Privacy policy|Modern Slavery Act Transparency Statement|Sitemap|About US| Contact US: help@patsnap.com