Dispersive/active dye combination printing compound paste and printing process thereof
A technology of reactive dyes and printing technology, which is applied in the field of fabric printing, can solve the problems of low washing fastness and poor hand feeling of paint printing, achieve high pattern definition, high structural viscosity, and improve the effect of use
- Summary
- Abstract
- Description
- Claims
- Application Information
AI Technical Summary
Problems solved by technology
Method used
Examples
Embodiment 1
[0021] 1) Prepare 2 parts of sodium alginate, 1 part of PTR, and 77 parts of water by weight;
[0022] After mixing the sodium alginate powder with a corresponding amount of water, fully stirring and mixing, and standing for 1.5 days to obtain 40 parts of sodium alginate paste with a mass content of 5% of sodium alginate; fully stirring and mixing with water to obtain 40 parts of sodium alginate paste with a mass content of 2.5%. PTR paste; mix sodium alginate paste and PTR paste in a mass ratio of 1:1 to obtain a composite paste;
[0023] 2) The disperse dark red SA-6B, reactive red HF-6BN, composite paste, sodium bicarbonate, urea and sodium m-nitrobenzene sulfonate are made into color paste for printing. After baking, steaming and washing, The compound paste consumption is 33% of the total material quality, the sodium bicarbonate consumption is 1.5% of the total material quality, the urea consumption is 6% of the total material quality, and the sodium m-nitrobenzene sulfona...
Embodiment 2
[0025] 1) Prepare 2 parts of sodium alginate, 1 part of PTR, and 77 parts of water by weight;
[0026] After mixing the sodium alginate powder with a corresponding amount of water, fully stirring and mixing, and standing for 1.5 days to obtain 38.5 parts of sodium alginate paste with a mass content of 5.2% of sodium alginate; fully stirring and mixing with water to obtain 41.5 parts of sodium alginate paste with a mass content of 2.4%. PTR paste; mix sodium alginate paste and PTR paste in a mass ratio of 1:1.08 to obtain a composite paste;
[0027] 2) Disperse orange SA-BR, active yellow HF-2GR, compound paste, sodium bicarbonate or sodium trichloroacetate, urea and sodium m-nitrobenzene sulfonate are made into color paste for printing, after baking, steaming It is obtained by steaming and washing; the dosage of composite paste is 32% of the total material mass, the dosage of sodium bicarbonate or sodium trichloroacetate is 1.45% of the total material mass, and the amount of u...
Embodiment 3
[0029] 1) Prepare 2 parts of sodium alginate, 1 part of PTR and 78 parts of water by weight;
[0030] Mix the sodium alginate powder with the corresponding amount of water, stir and mix thoroughly, and stand for 1 d to obtain 42.5 parts of sodium alginate paste with a mass content of 4.7% of sodium alginate; fully stir and mix with water to obtain 38.5 parts of PTR with a mass content of 2.6% paste; mix sodium alginate paste and PTR paste in a mass ratio of 1:0.9 to obtain a composite paste;
[0031] 2) The disperse navy blue SA-NB, reactive blue K-BF, composite paste, sodium bicarbonate or sodium trichloroacetate, urea and sodium m-nitrobenzene sulfonate are made into color paste for printing, after baking, steaming It is obtained by steaming and washing; the dosage of composite paste is 34% of the total material quality, the dosage of sodium bicarbonate or sodium trichloroacetate is 1.55% of the total material quality, and the amount of urea is 5.8% of the total material qua...
PUM
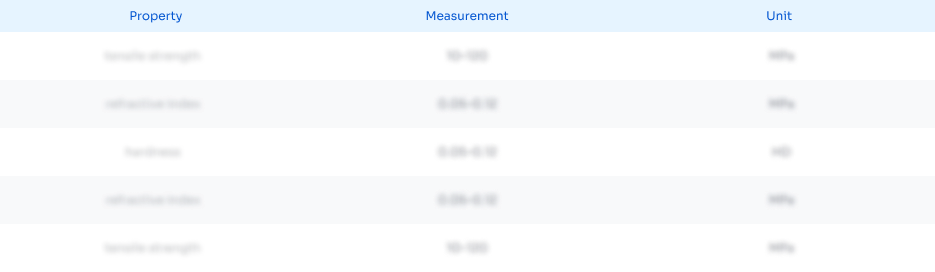
Abstract
Description
Claims
Application Information

- R&D
- Intellectual Property
- Life Sciences
- Materials
- Tech Scout
- Unparalleled Data Quality
- Higher Quality Content
- 60% Fewer Hallucinations
Browse by: Latest US Patents, China's latest patents, Technical Efficacy Thesaurus, Application Domain, Technology Topic, Popular Technical Reports.
© 2025 PatSnap. All rights reserved.Legal|Privacy policy|Modern Slavery Act Transparency Statement|Sitemap|About US| Contact US: help@patsnap.com