Smelting electric furnace waste heat recovery and recirculation system and method
A recycling system and waste heat recovery technology, applied in steam generation methods, furnaces, waste heat treatment, etc. using heat carrier, can solve the problems of low waste heat recovery efficiency, energy waste, etc., to improve recovery efficiency, reduce heat loss, work The effect of temperature reduction
- Summary
- Abstract
- Description
- Claims
- Application Information
AI Technical Summary
Problems solved by technology
Method used
Image
Examples
Embodiment Construction
[0015] The technical scheme of the present invention will be described in detail below in conjunction with the accompanying drawings.
[0016] Such as figure 2 As shown, a submerged arc furnace waste heat recovery and recycling system 200 according to the present invention includes a dust collector 210 , a waste heat boiler 220 , an induced draft fan 230 and a recirculation fan 240 . The dust collector is provided with a flue gas inlet 211 and a flue gas outlet 212, the waste heat boiler is provided with a flue gas inlet 221 and a flue gas outlet 222, and the induced draft fan is provided with a flue gas inlet 231 and a flue gas outlet 232, so The recirculation fan is provided with a flue gas inlet 241 and a flue gas outlet 242 .
[0017] The flue gas outlet 212 of the dust collector is connected to the flue gas inlet 221 of the waste heat boiler through the flue gas pipe, and the flue gas outlet 222 of the waste heat boiler is connected to the flue gas inlet 231 of the indu...
PUM
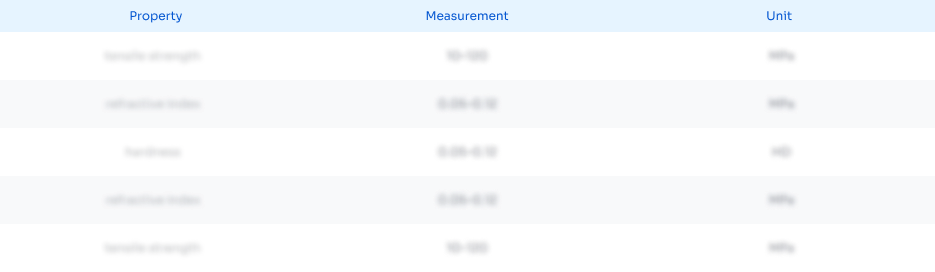
Abstract
Description
Claims
Application Information

- R&D Engineer
- R&D Manager
- IP Professional
- Industry Leading Data Capabilities
- Powerful AI technology
- Patent DNA Extraction
Browse by: Latest US Patents, China's latest patents, Technical Efficacy Thesaurus, Application Domain, Technology Topic, Popular Technical Reports.
© 2024 PatSnap. All rights reserved.Legal|Privacy policy|Modern Slavery Act Transparency Statement|Sitemap|About US| Contact US: help@patsnap.com