A driving device for automatic inspection and positioning of safety injection pipes of reactor pressure vessels
A pressure vessel and automatic inspection technology, which is applied to the monitoring of reactors and nuclear reactors, and the reduction of greenhouse gases, etc., can solve the problems of affecting the detection results, troublesome dismantling, and difficult root cleaning, etc., to achieve accurate positioning, tight and reliable effects
- Summary
- Abstract
- Description
- Claims
- Application Information
AI Technical Summary
Problems solved by technology
Method used
Image
Examples
Embodiment Construction
[0033] The present invention will be described in further detail below in conjunction with the accompanying drawings and specific embodiments.
[0034] Such as figure 1 As shown, the reactor pressure vessel safety injection pipe automatic inspection and positioning driving device includes a main movement assembly 7 at the rear end, an intermediate support assembly 3 at the front end, an axial assembly 2 at the safe end, and an inspection assembly 1 at the safe end.
[0035] As shown in Figure 2, the main motion assembly 7 is installed with a peripheral motion driving gear 25 and a peripheral motion driven gear 26 at the rear of the main motion sleeve 13, and a peripheral motor 24 and an axial motor 24 are installed on the main motion sleeve 13. motor27.
[0036] The stretching cylinder 23 installed at the front end of the main movement sleeve 13 and the fixed mount 12 are installed in the circumferential direction, and the piston rod of the stretched cylinder 23 passes throug...
PUM
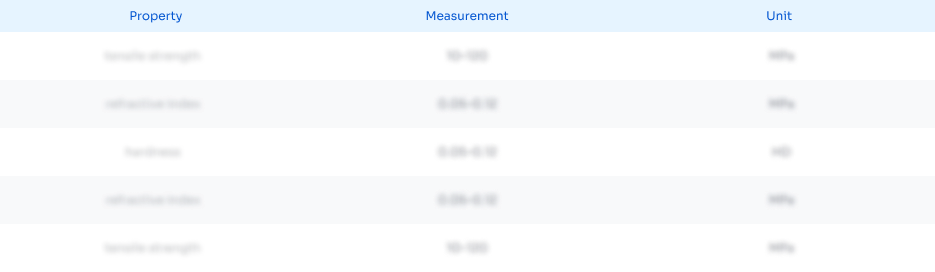
Abstract
Description
Claims
Application Information

- R&D Engineer
- R&D Manager
- IP Professional
- Industry Leading Data Capabilities
- Powerful AI technology
- Patent DNA Extraction
Browse by: Latest US Patents, China's latest patents, Technical Efficacy Thesaurus, Application Domain, Technology Topic, Popular Technical Reports.
© 2024 PatSnap. All rights reserved.Legal|Privacy policy|Modern Slavery Act Transparency Statement|Sitemap|About US| Contact US: help@patsnap.com