Multipath wire feed laser fused deposition modeling (LFDM) device and method
A laser melting and forming device technology, applied in the field of printing components, can solve problems such as broken wires and nozzle clogging, and achieve the effects of small heat-affected zone, efficient printing, and accelerated delivery of consumables
- Summary
- Abstract
- Description
- Claims
- Application Information
AI Technical Summary
Problems solved by technology
Method used
Image
Examples
Embodiment
[0030] Such as Figures 1 to 5 shown. The invention discloses a multi-channel wire feeding laser fusion deposition LFDM molding device, which includes a wire feeding nozzle 1 composed of a plurality of wire feeding pipelines 7, a wire feeding machine 12 for delivering the wire materials to the wire feeding pipeline 7, a laser Head 2, a carbon dioxide laser 8 connected to the laser head 2;
[0031] The wire feed nozzle 1 and the laser head 2 are fixed together by a connecting piece to form a composite printing head; a steering gear 6 is installed on the connecting piece to increase the degree of freedom of the composite printing head; the laser head 2 can emit a rectangular laser The beam is emitted from the side of the laser head 2, and irradiates and covers the end of the corresponding wire material 11 (consumable material) extending out of the wire feed nozzle 1, and melts it;
[0032] When multiple wire conveying pipes 7 work at the same time, by controlling the steering ...
PUM
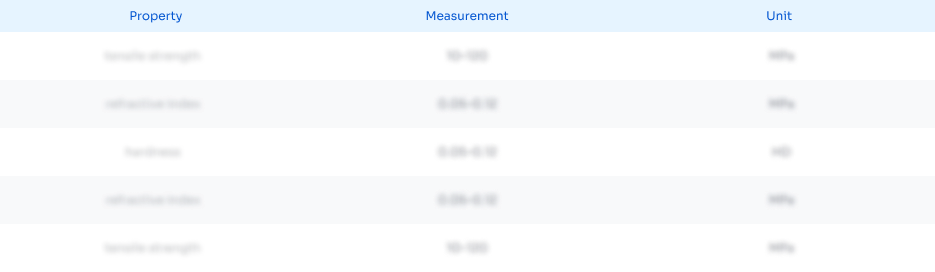
Abstract
Description
Claims
Application Information

- Generate Ideas
- Intellectual Property
- Life Sciences
- Materials
- Tech Scout
- Unparalleled Data Quality
- Higher Quality Content
- 60% Fewer Hallucinations
Browse by: Latest US Patents, China's latest patents, Technical Efficacy Thesaurus, Application Domain, Technology Topic, Popular Technical Reports.
© 2025 PatSnap. All rights reserved.Legal|Privacy policy|Modern Slavery Act Transparency Statement|Sitemap|About US| Contact US: help@patsnap.com