LED lighting heat sink and method for manufacturing same
A technology of LED lighting and cooling fins, which is applied in lighting and heating equipment, cooling/heating devices of lighting devices, lighting devices, etc., can solve the problems of high manufacturing costs, complex molds, and needs, so as to reduce manufacturing costs and realize Part structure, effect of high dimensional accuracy
- Summary
- Abstract
- Description
- Claims
- Application Information
AI Technical Summary
Problems solved by technology
Method used
Image
Examples
no. 3 approach
[0110] image 3 A third embodiment of the heat sink for LED lighting according to the present invention is shown. image 3 Heat sink 1 shown for LED lighting with figure 2 Similarly, a metal thin plate 1 having a constant plate thickness such as aluminum is integrally formed, and as figure 2 Thus, the whole has a hollow square tube shape (square tube cup shape). figure 2 The heat sink 1 for LED lighting of the present invention is different from the above-mentioned point in that the LED element mounting surface 2 and the heat dissipation side surface 3 are integrally formed from a single metal sheet by drawing processing. figure 1 , 2 The situation is the same.
[0111] Should image 3 The heat sink 1 for LED lighting has an LED component mounting surface 2 and four heat dissipation side surfaces 4, 5, 6, and 7 that are planar, and is formed in the Y direction (up and down) of the drawings with a section higher than the LED component mounting surface 2. direction) and ...
no. 4 approach
[0120] Figure 4 A fourth embodiment of the heat sink for LED lighting according to the present invention is shown. Figure 4 Heat sink 1 shown for LED lighting is with figure 2 Same overall shape, but no figure 2 Like the opening 10 on the bottom side, the heat dissipation side 6 in the cylinder has an opening (space) 11 in which the internal space of the cylindrical body is opened to the outside without actually having a heat dissipation side.
[0121] The opening 11 is provided within a range that does not hinder the rigidity of the heat sink 1 , and can have a larger area than the heat radiation side area of the heat sink 1 in cooperation with the opening 10 on the bottom side. Therefore, the convection function between the air in the internal space and the outside air through the openings 10 and 11 inside and outside the heat sink 1 is improved. As a result, with figure 2 Compared with the case where the heat dissipation side surface 6 is not provided, the area o...
PUM
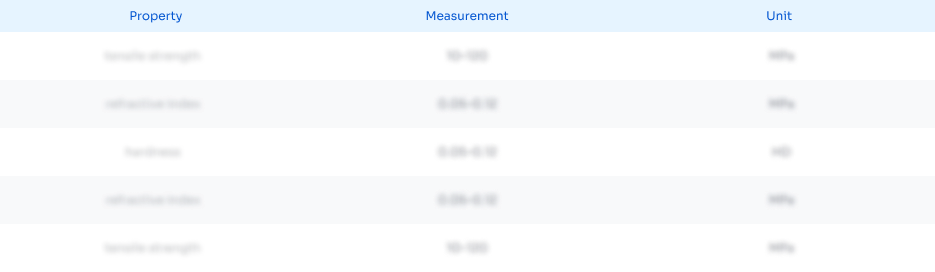
Abstract
Description
Claims
Application Information

- R&D
- Intellectual Property
- Life Sciences
- Materials
- Tech Scout
- Unparalleled Data Quality
- Higher Quality Content
- 60% Fewer Hallucinations
Browse by: Latest US Patents, China's latest patents, Technical Efficacy Thesaurus, Application Domain, Technology Topic, Popular Technical Reports.
© 2025 PatSnap. All rights reserved.Legal|Privacy policy|Modern Slavery Act Transparency Statement|Sitemap|About US| Contact US: help@patsnap.com