A double deflection implicit Lorentz force deflection magnetic bearing
A Lorentz force and magnetic bearing technology, applied in the field of non-contact magnetic suspension bearings, can solve the problems of reducing the magnetic density uniformity, the air gap magnetic density is small, reducing the air gap magnetic density uniformity, etc., to increase the air gap magnetic field strength. And, improve the uniformity of magnetic density and eliminate the effect of magnetic density fluctuation
- Summary
- Abstract
- Description
- Claims
- Application Information
AI Technical Summary
Problems solved by technology
Method used
Image
Examples
specific Embodiment approach
[0017] The preferred embodiment of the double deflection implicit Lorentz force deflection magnetic bearing of the present invention is:
[0018]It is mainly composed of a rotor system and a stator system. The rotor system mainly includes: outer mounting sleeve, outer upper magnetic ring, outer middle magnetic ring, outer lower magnetic ring, outer upper magnet, outer middle upper magnet, outer middle lower Magnetic steel, outer and lower magnetic steel, outer and upper magnetic ring, outer, middle and upper magnetic ring, outer, middle and lower magnetic ring, outer and lower magnetic ring, outer and upper magnetic lock mother, outer and lower magnetic lock mother, guide disk , turntable, outer component lock nut, inner mounting sleeve, inner upper magnetic ring, inner middle magnetic ring, inner lower magnetic ring, inner upper magnetic steel, inner middle upper magnetic steel, inner middle lower magnetic steel, inner lower magnetic Steel, inner upper magnetic isolation ring...
specific Embodiment
[0022] like figure 1 , figure 2As shown, it is mainly composed of a rotor system and a stator system. The rotor system mainly includes: outer mounting sleeve 1, outer upper magnetic ring 2A, outer middle magnetic ring 2B, outer lower magnetic ring 2C, outer upper magnetic steel 3A, outer Upper middle magnetic steel 3B, outer middle lower magnetic steel 3C, outer lower magnetic steel 3D, outer upper magnetic ring 4A, outer middle upper magnetic ring 4B, outer middle lower magnetic ring 4C, outer lower magnetic ring 4D, outer Upper magnetic lock nut 5A, outer and lower magnetic lock nut 5B, magnetic disc 6, turntable 7, outer component lock nut 8, inner mounting sleeve 9, inner upper magnetic ring 10A, inner middle magnetic ring 10B, inner lower guide Magnetic ring 10C, inner upper magnetic steel 11A, inner middle upper magnetic steel 11B, inner middle lower magnetic steel 11C, inner lower magnetic steel 11D, inner upper magnetic ring 12A, inner middle upper magnetic ring 12B,...
PUM
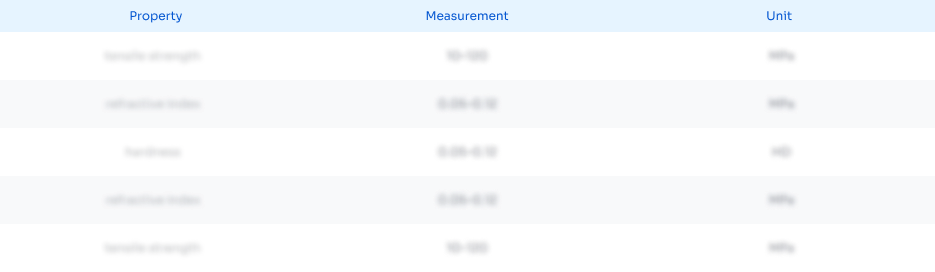
Abstract
Description
Claims
Application Information

- Generate Ideas
- Intellectual Property
- Life Sciences
- Materials
- Tech Scout
- Unparalleled Data Quality
- Higher Quality Content
- 60% Fewer Hallucinations
Browse by: Latest US Patents, China's latest patents, Technical Efficacy Thesaurus, Application Domain, Technology Topic, Popular Technical Reports.
© 2025 PatSnap. All rights reserved.Legal|Privacy policy|Modern Slavery Act Transparency Statement|Sitemap|About US| Contact US: help@patsnap.com