Curing agent prepared from TMPTA production wastewater and method of curing agent
A technology for curing agent and waste water is applied in the field of curing agent prepared by using TMPTA waste water, which can solve the problems of secondary pollution, waste, and large energy consumption.
- Summary
- Abstract
- Description
- Claims
- Application Information
AI Technical Summary
Problems solved by technology
Method used
Examples
Embodiment 1
[0022] S1: Concentrate 50 parts of TMPTA industrial wastewater by evaporation under reduced pressure to a sodium acrylate concentrate with a sodium acrylate content of 35%;
[0023] S2: Add 10 parts of 4-acetylaminosalicylic acid, 3 parts of L-cysteine, 8 parts of 2-ethylhexyl salicylate, and 6 parts of ethyl acetate to step S1, and raise the temperature to 60 ℃, keep warm for 20 minutes;
[0024] S3: Add 9 parts of 5-nitrofurfural diacetate, 3 parts of 2-thiophene carboxaldehyde, and 7 parts of dimercaprol into step S2, continue to raise the temperature to 80°C, and stir and react at a rate of 800r / min for 1h;
[0025] S4: Add 2 parts of 5-hydroxytryptamine and 4 parts of eugenol to step S3, stir for 5 minutes, and react with microwave at a power of 3500W for 20 minutes; the curing agent can be obtained after the reaction is cooled.
Embodiment 2
[0031] S1: Concentrate 80 parts of TMPTA industrial wastewater by vacuum evaporation to a sodium acrylate concentrate with a sodium acrylate content of 55%;
[0032] S2: Add 15 parts of 4-acetylaminosalicylic acid, 8 parts of L-cysteine, 12 parts of 2-ethylhexyl salicylate, and 10 parts of ethyl acetate to step S1, and raise the temperature to 80 ℃, keep warm for 40 minutes;
[0033] S3: Add 14 parts of 5-nitrofurfural diacetate, 6 parts of 2-thiophene carboxaldehyde, and 12 parts of dimercaprol into step S2, continue to raise the temperature to 110°C, and stir and react at a rate of 1200r / min for 2h;
[0034] S4: Add 5 parts of 5-hydroxytryptamine and 8 parts of eugenol to step S3, stir for 15 minutes, and react with microwave at a power of 3500W for 30 minutes; the curing agent can be obtained after the reaction is cooled.
Embodiment 3
[0040] S1: Concentrate 60 parts of TMPTA industrial wastewater by evaporation under reduced pressure to a sodium acrylate concentrate with a sodium acrylate content of 35%;
[0041] S2: Add 11 parts of 4-acetylaminosalicylic acid, 4 parts of L-cysteine, 9 parts of 2-ethylhexyl salicylate, and 7 parts of ethyl acetate to step S1, and raise the temperature to 60 ℃, keep warm for 40 minutes;
[0042] S3: Add 10 parts of 5-nitrofurfural diacetate, 4 parts of 2-thiophene carboxaldehyde, and 8 parts of dimercaprol into step S2, continue to raise the temperature to 90° C., and stir for 2 hours at a rate of 800 r / min;
[0043] S4: Add 3 parts of 5-hydroxytryptamine and 5 parts of eugenol to step S3, stir for 10 minutes, and react with microwave at a power of 3500W for 30 minutes; the curing agent can be obtained after the reaction is cooled.
PUM
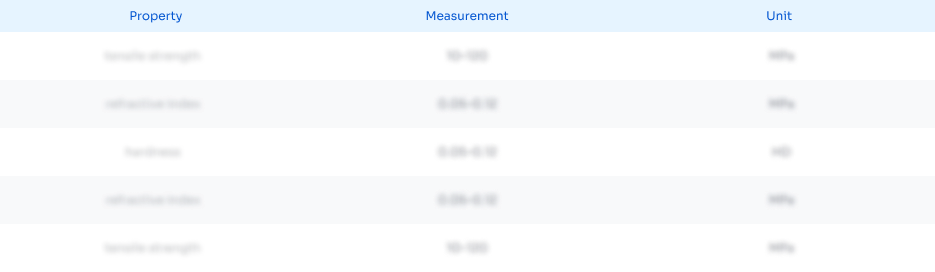
Abstract
Description
Claims
Application Information

- Generate Ideas
- Intellectual Property
- Life Sciences
- Materials
- Tech Scout
- Unparalleled Data Quality
- Higher Quality Content
- 60% Fewer Hallucinations
Browse by: Latest US Patents, China's latest patents, Technical Efficacy Thesaurus, Application Domain, Technology Topic, Popular Technical Reports.
© 2025 PatSnap. All rights reserved.Legal|Privacy policy|Modern Slavery Act Transparency Statement|Sitemap|About US| Contact US: help@patsnap.com