Automatic wire harness machine
A technology of automatic line and main motor, applied in the direction of electrical components, circuits, conductor/cable insulation, etc., to achieve precise assembly, efficient assembly work, and reduce labor requirements
- Summary
- Abstract
- Description
- Claims
- Application Information
AI Technical Summary
Problems solved by technology
Method used
Image
Examples
Embodiment 1
[0017] When the winding work has not yet started, the main switch 25 is turned off, and the traction block 3 is located at the rear end of the base 7. At this time, one end of the wire harness 8 to be processed is firstly wound with the tape roll 11 twice, and then passed through the fixing sleeve 20. Install the hole forward on the wire clamping vise 4, turn the crank 5 to clamp the wire harness, install the tape roll 11 on the tape seat 10, draw out a certain length of tape, and wrap it twice on the corresponding position of the wire harness to be processed. , turn on the auxiliary motor steering and stop switch 24, and then turn on the main switch 25. At this time, the main motor 1 and the auxiliary motor start to work, and the main motor drives the traction block 3, the clamping vise 4 and the wire harness 8 to be processed to move forward, and at the same time The auxiliary motor 21 drives the pulley 12 through the belt 13 to rotate the sleeve 6, the tape seat 10 and the t...
Embodiment 2
[0020] At the beginning of this stroke, the traction block 3 and the wire clamping vise 4 are at the front end of the base, turn on the main switch 25 and the main motor 1 starts to rotate, the traction block 3 and the wire clamping vise 4 move to the rear end of the base, at this time the auxiliary The motor and the wire harness 8 to be processed are in a stopped state. When the traction block 3 and the wire clamping vise 4 move to the sensing range of the rear travel switch 23 at the rear end of the base, the rear travel switch 23 sends a steering signal to the main motor controller 16. The main motor 1 starts to rotate in the forward direction. At this time, the main switch of the circuit needs to be turned off, so that the main and auxiliary motors all stop rotating. This time the return stroke is over.
Embodiment 3
[0022] At the beginning of this stroke, the traction block 3 is at the rear end of the base 7. At this time, it is necessary to install the wire harness 8 that needs to be processed beside it on the wire clamping vise, rotate the crank 5 to clamp the wire harness and fix it, turn on the auxiliary motor steering And stop switch 24, then turn on the main switch 25, at this time the main motor 1 and the screw shaft 2 start to rotate, driving the traction block 3 and the wire harness 8 to be processed to move forward, and the auxiliary motor 21 starts to work, driving the pulley through the belt 13. 12. The rotating sleeve 6, the tape base 10 and the tape roll 11 rotate around the wire harness 8 to be processed, and the next working stroke starts, and so on and so forth.
[0023] In particular, the speed adjustment switches of the main and auxiliary motors can be adjusted only once under normal circumstances. When the winding speed is found to be too fast or too slow, and the windi...
PUM
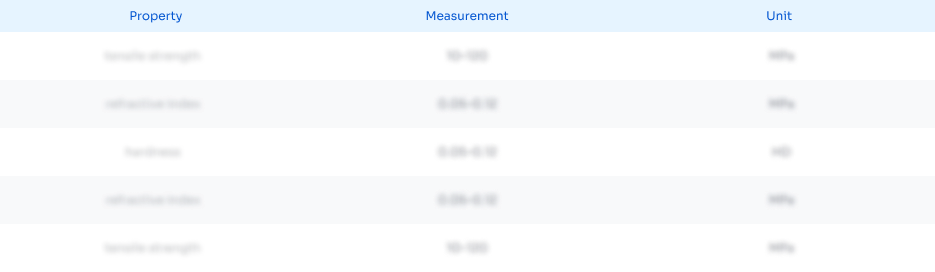
Abstract
Description
Claims
Application Information

- R&D Engineer
- R&D Manager
- IP Professional
- Industry Leading Data Capabilities
- Powerful AI technology
- Patent DNA Extraction
Browse by: Latest US Patents, China's latest patents, Technical Efficacy Thesaurus, Application Domain, Technology Topic, Popular Technical Reports.
© 2024 PatSnap. All rights reserved.Legal|Privacy policy|Modern Slavery Act Transparency Statement|Sitemap|About US| Contact US: help@patsnap.com