High-pressure fixed bed alkylation method for mixed m-cresol and p-cresol
A technology of p-cresol and fixed bed is applied in the field of separation of p-cresol between mixed materials, which can solve the problems of low utilization rate of raw materials, long reaction time, subsequent separation of unfavorable products, etc. Conversion rate boost
- Summary
- Abstract
- Description
- Claims
- Application Information
AI Technical Summary
Problems solved by technology
Method used
Image
Examples
Embodiment 1
[0039] Alkylation agent composition: butane volume content 70% isobutene content 30%;
[0040] Fixed bed reactor operating pressure: 1.7MPa;
[0041] Fixed bed reactor operating temperature: 50°C
[0042] Airspeed: 0.1h -1
[0043] Molar ratio isobutylene: mixed phenol = 0.5:1
[0044] Mass fraction of p-cresol: 10%
[0045] 100ml of catalyst is filled in a single-stage fixed-bed reactor with an inner diameter of 25mm and a height of 400mm;
[0046] The first step: the determination of each flow
[0047] Because the space velocity of the fixed bed reactor is 0.1h -1 , the amount of catalyst is 100ml, according to the formula
[0048]
[0049] Where V is the catalyst volume, τ is the space velocity, a is the molar ratio of enphenol, b is the volume fraction of isobutene, M 1 and ρ 1 is the molar mass and density of isobutene, M 2 and ρ 2 is the molar mass and density of cresol, V 1 is the volume flow rate of isobutene, V 2 Be the volume flow of mixing p-cresol; (f...
Embodiment 2
[0054] Alkylating agent composition: butane content 80% isobutene content 20%
[0055] Fixed bed reactor operating pressure: 4.2MPa
[0056] Fixed bed reactor operating temperature: 70°C
[0057] Airspeed: 4.2h -1
[0058] Enol molar ratio: 2:1
[0059] Mass fraction of p-cresol: 50%
[0060] Reactor used and catalyst loading are the same as embodiment one
[0061] The first step: the determination of each flow
[0062] Because the space velocity of the fixed bed reactor is 4.2h -1 , the amount of catalyst is 100ml, calculated by the formula in Example 1, the flow rate of mixed phenol is 46.33ml / h, the flow rate of isobutene is 74.73ml / h, the flow rate of butane is 298.94ml / h, and the flow rate of isobutane and propane is 0;
[0063] The second step: Alkylation reaction
[0064] Adjust the parameters of each flowmeter according to the above calculation results, and at the same time pressurize and liquefy the isobutylene and additives separately and mix them fully, inje...
Embodiment 3
[0066] Alkylating agent composition: butane content 90% isobutene content 10%
[0067] Fixed bed reactor reaction pressure: 4.2MPa
[0068] Fixed bed reactor operating temperature: 110°C
[0069] Airspeed: 5h -1
[0070] Enol molar ratio: 3:1
[0071] Mass fraction of p-cresol: 90%
[0072] Reactor used and catalyst loading are the same as embodiment one
[0073] The first step: the determination of each flow
[0074] Because the fixed bed reactor space velocity is 5h -1 , the amount of catalyst is 100ml, calculated by the formula in Example 1, the flow rate of mixed phenol is 19.85ml / h, the flow rate of isobutene is 48.02ml / h, the flow rate of butane is 432.13ml / h, and the flow rate of isobutane and propane is 0;
[0075] The second step: Alkylation reaction
[0076] Adjust the parameters of each flowmeter according to the above calculation results, and at the same time pressurize and liquefy the isobutylene and additives separately and mix them fully, inject them tog...
PUM
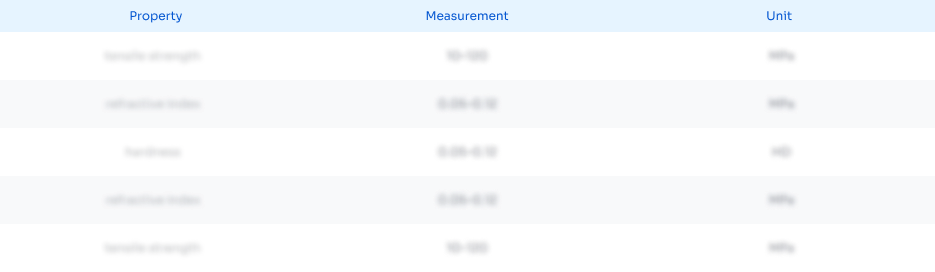
Abstract
Description
Claims
Application Information

- Generate Ideas
- Intellectual Property
- Life Sciences
- Materials
- Tech Scout
- Unparalleled Data Quality
- Higher Quality Content
- 60% Fewer Hallucinations
Browse by: Latest US Patents, China's latest patents, Technical Efficacy Thesaurus, Application Domain, Technology Topic, Popular Technical Reports.
© 2025 PatSnap. All rights reserved.Legal|Privacy policy|Modern Slavery Act Transparency Statement|Sitemap|About US| Contact US: help@patsnap.com