Ceramic firing method
A technology of ceramics and ceramic blanks, which is applied in the field of ceramic manufacturing, can solve problems such as poor load-bearing capacity, low mud plate strength, deformation, etc., and achieve the effects of improving firing pass rate, solving deformation problems, and reducing costs
- Summary
- Abstract
- Description
- Claims
- Application Information
AI Technical Summary
Problems solved by technology
Method used
Image
Examples
Embodiment 1
[0045] A ceramic firing method, comprising:
[0046] 1. Install the first kiln panel 110 horizontally in the kiln.
[0047] 2. A plurality of high temperature resistant ceramic balls 130 are laid on the first kiln plate 110 .
[0048] 3. Lay two second kiln panels 120 on a plurality of high-temperature-resistant ceramic balls 130, and the gap between adjacent second kiln panels is 35 mm.
[0049] 3. Place the ceramic green body 2 on the second kiln board 120 so that the bottom is evenly supported by the two second kiln boards 120 .
[0050] 4. On the first kiln plate 110, a stop frame 140 for limiting the position outside the high-temperature-resistant ceramic ball 130 is provided, and its thickness is 15 mm.
[0051] 5. Start the kiln to fire the ceramic green body 2 at a firing temperature of 1300° C. for 8 hours.
[0052] The ceramic green body fired in this embodiment is in the shape of a pair of long strips, and the shrinkage of the narrower side can be ignored, so two...
Embodiment 2
[0054] A ceramic firing method, comprising:
[0055] 1. Install the first kiln panel 110 horizontally in the kiln.
[0056] 2. Lay a plurality of high temperature resistant alumina balls 130 on the first kiln plate 110 .
[0057] 3. Lay four second kiln panels 120 in a 2×2 matrix on multiple high-temperature-resistant alumina balls 130, and the gap between adjacent second kiln panels is 30mm.
[0058] 3. Place the ceramic green body 2 on the second kiln board 120 so that the bottom thereof is evenly supported by four second kiln boards 120 .
[0059] 4. On the first kiln plate 110, a stop frame 140 for limiting the position outside the high-temperature-resistant alumina ball 130 is provided, and its thickness is 16mm.
[0060] 5. Start the kiln to fire the ceramic green body 2 at a firing temperature of 1200° C. for 7 hours.
[0061] The ceramic body fired in this embodiment has a regular shape with almost the same length and width, so four second kiln plates 120 are select...
PUM
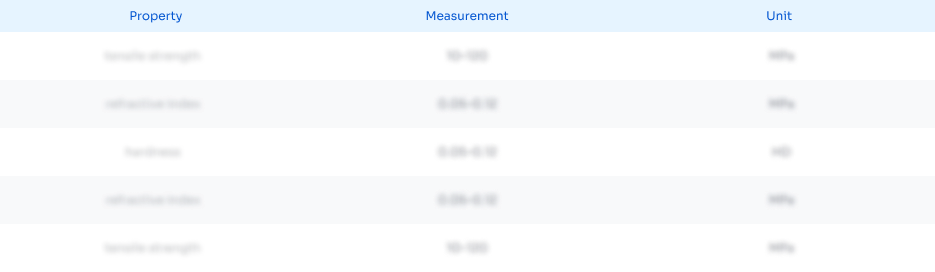
Abstract
Description
Claims
Application Information

- R&D
- Intellectual Property
- Life Sciences
- Materials
- Tech Scout
- Unparalleled Data Quality
- Higher Quality Content
- 60% Fewer Hallucinations
Browse by: Latest US Patents, China's latest patents, Technical Efficacy Thesaurus, Application Domain, Technology Topic, Popular Technical Reports.
© 2025 PatSnap. All rights reserved.Legal|Privacy policy|Modern Slavery Act Transparency Statement|Sitemap|About US| Contact US: help@patsnap.com