A kind of iron mineral inhibitor and preparation method thereof
A production method and inhibitor technology, applied in solid separation, flotation, etc., can solve the problems of lower tailings grade, weak suppression ability, and weak action ability of fine-grained iron minerals, so as to reduce flotation tailings, The effect of strengthening the effective effect and increasing the ability of action
- Summary
- Abstract
- Description
- Claims
- Application Information
AI Technical Summary
Problems solved by technology
Method used
Examples
Embodiment 1
[0064] In the first step, a mixture of the following components by weight is reacted at 82°C to 85°C for 2 hours to obtain high-efficiency additive 1:
[0065] 100 parts cornstarch
[0066] Sodium ethylate catalyst 0.8 part
[0067] Sodium Chloroacetate 8 parts
[0068] In the second step, the high-efficiency additive 2 is obtained by reacting the mixture of the following components in parts by weight at 73°C to 75°C for 4 to 5 hours:
[0069] 1 100 parts of high-efficiency additives obtained by the above-mentioned first step
[0070] 8 parts of ethylene oxide
[0071] Sodium acetate catalyst 0.6 parts
[0072] The third step is to obtain the finished inhibitor product by reacting the mixture of the following components by weight at 52°C to 55°C for 2 to 3 hours:
[0073] 100 parts of high-efficiency auxiliary agent 2 obtained by the above-mentioned second step
[0074] 3 parts sodium periodate
[0075] Copper sulfate catalyst 0.4 parts
[0076] Product performance: Co...
Embodiment 2
[0078] In the first step, a mixture of the following components by weight is reacted at 82°C to 85°C for 2 hours to obtain high-efficiency additive 1:
[0079] Tapioca starch 100 parts
[0080] Sodium hydroxide catalyst 3.0 parts
[0081] Sodium Chloroacetate 10 parts
[0082] In the second step, the high-efficiency additive 2 is obtained by reacting the mixture of the following components in parts by weight at 72°C to 75°C for 4 to 5 hours:
[0083] 1 100 parts of high-efficiency additives obtained by the above-mentioned first step
[0084] 8 parts of ethylene oxide
[0085] Sodium carbonate catalyst 0.6 parts
[0086] The third step is to obtain the finished inhibitor product by reacting the mixture of the following components by weight at 52°C to 55°C for 2 to 3 hours:
[0087] 100 parts of high-efficiency auxiliary agent 2 obtained by the above-mentioned second step
[0088] 9 parts hydrogen peroxide
[0089] Ferrous sulfate catalyst 0.4 part
[0090] Product perform...
Embodiment 3
[0092] In the first step, a mixture of the following components by weight is reacted at 82°C to 85°C for 2 hours to obtain high-efficiency additive 1:
[0093] 100 parts wheat starch
[0094] Sodium hydroxide catalyst 3.0 parts
[0095] Sodium Chloroacetate 10 parts
[0096] In the second step, the high-efficiency additive 2 is obtained by reacting the mixture of the following components in parts by weight at 73°C to 75°C for 4 to 5 hours:
[0097] 1 100 parts of high-efficiency additives obtained by the above-mentioned first step
[0098] 8 parts of ethylene oxide
[0099] Sodium carbonate catalyst 0.8 part
[0100] The third step is to obtain the finished inhibitor by reacting the mixture of the following components by weight at 53°C to 55°C for 2 to 3 hours:
[0101] 100 parts of high-efficiency auxiliary agent 2 obtained by the above-mentioned second step
[0102] 9 parts hydrogen peroxide
[0103] Ferrous sulfate catalyst 0.4 part
[0104] Product performance: Com...
PUM
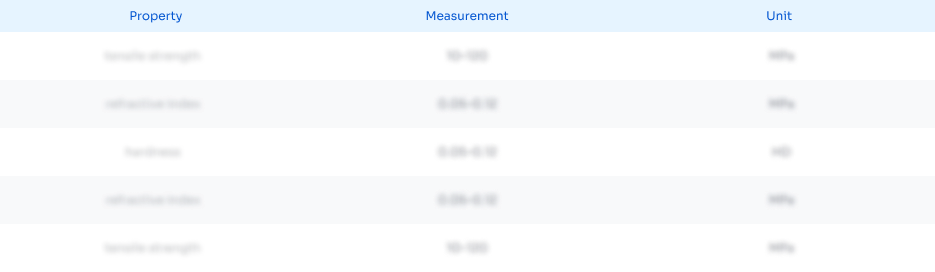
Abstract
Description
Claims
Application Information

- R&D
- Intellectual Property
- Life Sciences
- Materials
- Tech Scout
- Unparalleled Data Quality
- Higher Quality Content
- 60% Fewer Hallucinations
Browse by: Latest US Patents, China's latest patents, Technical Efficacy Thesaurus, Application Domain, Technology Topic, Popular Technical Reports.
© 2025 PatSnap. All rights reserved.Legal|Privacy policy|Modern Slavery Act Transparency Statement|Sitemap|About US| Contact US: help@patsnap.com