Method for stabilizing specific surface area of grinding powder
A specific surface area and grinding technology, which is applied in cement production, grain processing, etc., can solve the problems of manpower and material resources consumption, energy waste, control lag, etc., and achieve the effect of reducing labor intensity, improving control effect, and ensuring smooth operation
- Summary
- Abstract
- Description
- Claims
- Application Information
AI Technical Summary
Problems solved by technology
Method used
Image
Examples
Embodiment Construction
[0030] In order to further explain the features of the present invention, please refer to the following detailed description and drawings of the present invention. The attached drawings are for reference and explanation purposes only, and are not used to limit the protection scope of the present invention.
[0031] Such as Figure 1 to Figure 2 As shown, this embodiment discloses a method for stabilizing the specific surface area of the powder body, including the following steps S1 to S6:
[0032] S1, real-time collection of the specific surface area of the powder body and the speed of the separator;
[0033] In practical applications, first use an online particle size analyzer installed in the grinding head to sample the incoming powder in real time, and detect the specific surface area of the incoming powder, and read the speed of the separator in real time from the frequency converter.
[0034] S2. Determine the pure lag time and inertia process time for the speed of the powd...
PUM
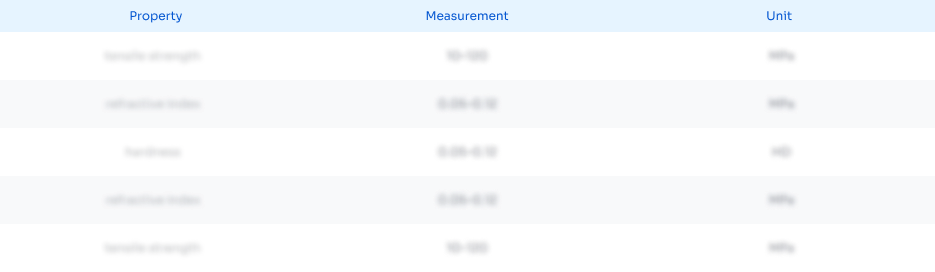
Abstract
Description
Claims
Application Information

- Generate Ideas
- Intellectual Property
- Life Sciences
- Materials
- Tech Scout
- Unparalleled Data Quality
- Higher Quality Content
- 60% Fewer Hallucinations
Browse by: Latest US Patents, China's latest patents, Technical Efficacy Thesaurus, Application Domain, Technology Topic, Popular Technical Reports.
© 2025 PatSnap. All rights reserved.Legal|Privacy policy|Modern Slavery Act Transparency Statement|Sitemap|About US| Contact US: help@patsnap.com