Method for optimizing dynamic performance of entire numerical control machine tool
A technology of dynamic performance and CNC machine tools, which is applied in the directions of multi-objective optimization, design optimization/simulation, electrical digital data processing, etc., can solve the problem that there are few research methods, the characteristics of the machine tool joint are not considered, and it is not enough to determine whether the dynamic model of the whole machine is Correct and other issues
- Summary
- Abstract
- Description
- Claims
- Application Information
AI Technical Summary
Problems solved by technology
Method used
Image
Examples
Embodiment Construction
[0077] In order to understand the present invention more clearly, the following will further discuss the present invention in detail in combination with the accompanying drawings and the examples completed by the inventor according to the technical solution of the present invention.
[0078] Identification of dynamic parameters of bolt joint
[0079] The distribution of spring-damping units between the joint surfaces of bolted connections is determined by the number of bolts, the type of bolts and the area of the joint surfaces. The column-bed joint is a key bolt joint in the machine tool structure. Taking it as an example, the identification process of the dynamic parameters of the joint is as follows.
[0080] 1. Build an equivalent bolt structure
[0081] The bed-column bolt joint in the machine tool structure is as follows: figure 1 As shown, three M20 bolts are symmetrically distributed on both sides, and the bolt tightening torque is 500N·m. The contact surface pres...
PUM
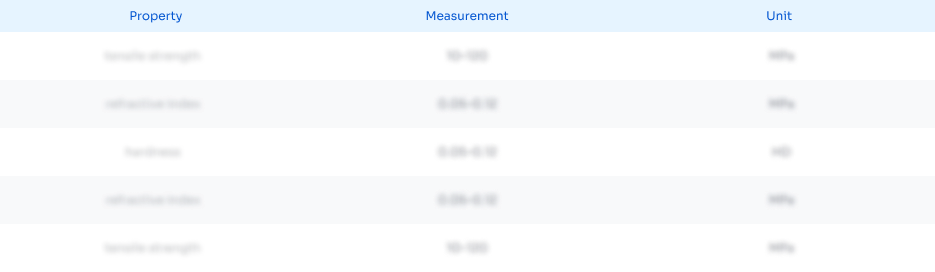
Abstract
Description
Claims
Application Information

- Generate Ideas
- Intellectual Property
- Life Sciences
- Materials
- Tech Scout
- Unparalleled Data Quality
- Higher Quality Content
- 60% Fewer Hallucinations
Browse by: Latest US Patents, China's latest patents, Technical Efficacy Thesaurus, Application Domain, Technology Topic, Popular Technical Reports.
© 2025 PatSnap. All rights reserved.Legal|Privacy policy|Modern Slavery Act Transparency Statement|Sitemap|About US| Contact US: help@patsnap.com