Ultrasonic method for measuring residual stress of cambered workpiece
A technology for measuring curved surfaces and residual stress. It is applied in the direction of measuring force, measuring device, and analyzing solids using sonic/ultrasonic/infrasonic waves. Effect
- Summary
- Abstract
- Description
- Claims
- Application Information
AI Technical Summary
Problems solved by technology
Method used
Image
Examples
Embodiment
[0030] A method for measuring the residual stress of a curved surface workpiece by ultrasonic method, comprising the following steps:
[0031] S1. Make a zero-stress flat plate calibration block of the same material as the curved surface workpiece to be tested for ultrasonic stress testing, change the propagation distance x of the critical refracted longitudinal wave in the zero-stress flat plate calibration block and measure the propagation time t corresponding to the propagation distance x 0x , to obtain the propagation distance x and the propagation time t of the critical refracted longitudinal wave in the zero stress flat plate calibration block 0x relational database and fit the function curve t of the two 0x =M(x);
[0032] S2. Apply stress σ on the zero-stress flat plate calibration block to perform ultrasonic stress test; change the propagation distance x of the critical refracted longitudinal wave in the flat plate calibration block under the σ stress state and measu...
PUM
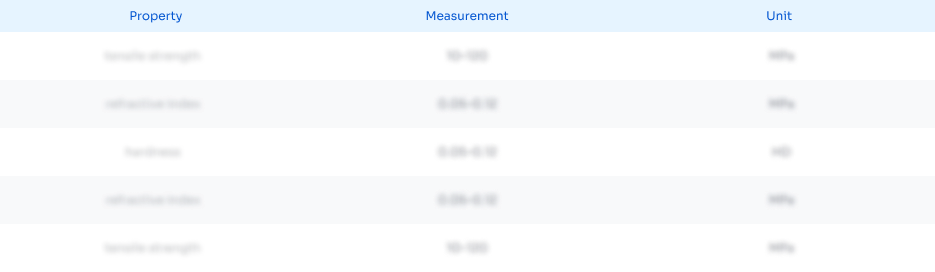
Abstract
Description
Claims
Application Information

- R&D
- Intellectual Property
- Life Sciences
- Materials
- Tech Scout
- Unparalleled Data Quality
- Higher Quality Content
- 60% Fewer Hallucinations
Browse by: Latest US Patents, China's latest patents, Technical Efficacy Thesaurus, Application Domain, Technology Topic, Popular Technical Reports.
© 2025 PatSnap. All rights reserved.Legal|Privacy policy|Modern Slavery Act Transparency Statement|Sitemap|About US| Contact US: help@patsnap.com