Large-current connection plug bush
A high-current, plug-in technology, applied in the direction of connection, parts and circuits of connecting devices, can solve the problems of easy blackening, easy detachment, and difficulty in bearing the impact of large current at the contact point, so as to strengthen the floating support and The effect of connecting, ensuring the insertion angle, and increasing the contact area
- Summary
- Abstract
- Description
- Claims
- Application Information
AI Technical Summary
Problems solved by technology
Method used
Image
Examples
Embodiment 1
[0027] Embodiment 1: refer to Figure 1 to Figure 3 , high-current connection socket, including bushing 1, reed 2 inside bushing 1, the front end of bushing 1 is provided with conductive front end cover 3, the materials of front end cover 3 and bushing 1 are brass, and the front end cover The outer diameter of 3 is consistent with the outer diameter of casing 1, and the front end cover 3 is fixedly connected with casing 1, and eight quadrilateral pit-shaped closing structures 5 are stamped at the joint through closing equipment, and the closing structure 5 can strengthen the front end cover 3 more than The connection between the sleeves 1 prevents loosening between the front cover 3 and the sleeves after long-term plugging and unplugging. The front cover 3 and the sleeve 1 form a hollow cavity. The front end of the front cover 3 is provided with an opening. There is a 45° chamfer structure, the reed 2 is set in the hollow cavity, the outer sleeve of the reed 2 is provided with...
Embodiment 2
[0029] Embodiment 2: refer to Figure 1 to Figure 3, high-current connection socket, including bushing 1, reed 2 inside bushing 1, the front end of bushing 1 is provided with conductive front end cover 3, the materials of front end cover 3 and bushing 1 are brass, and the front end cover The outer diameter of 3 is consistent with the outer diameter of casing 1, and the front end cover 3 is fixedly connected with casing 1, and the joint is stamped with four line-segment-shaped concave closing structures 5 through closing equipment, and the closing structure 5 can strengthen the front cover 3 and other casings 1 connection to avoid loosening between the front cover 3 and the casing after long-term plugging and use. The front cover 3 and the casing 1 form a hollow cavity. The front end of the front cover 3 is provided with an opening. ° chamfering structure, the reed 2 is set in the hollow cavity, the reed 2 is provided with an inner bushing 4, and the inner bushing 4 is provided...
Embodiment 3
[0031] Embodiment 3: refer to Figure 1 to Figure 3 , high-current connection socket, including bushing 1, reed 2 inside bushing 1, the front end of bushing 1 is provided with conductive front end cover 3, the materials of front end cover 3 and bushing 1 are brass, and the front end cover The outer diameter of 3 is consistent with the outer diameter of casing 1, and the front end cover 3 is fixedly connected with casing 1, and eight rectangular pit-shaped closing structures 5 are stamped at the joint through closing equipment, and the closing structure 5 can strengthen the front end cover 3 more than The connection between the sleeves 1 prevents loosening between the front cover 3 and the sleeves after long-term plugging and unplugging. The front cover 3 and the sleeve 1 form a hollow cavity. The front end of the front cover 3 is provided with an opening. There is a 45° chamfer structure, the reed 2 is set in the hollow cavity, the outer sleeve of the reed 2 is provided with a...
PUM
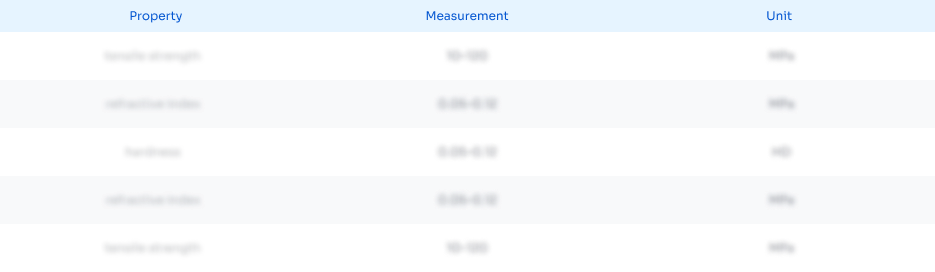
Abstract
Description
Claims
Application Information

- Generate Ideas
- Intellectual Property
- Life Sciences
- Materials
- Tech Scout
- Unparalleled Data Quality
- Higher Quality Content
- 60% Fewer Hallucinations
Browse by: Latest US Patents, China's latest patents, Technical Efficacy Thesaurus, Application Domain, Technology Topic, Popular Technical Reports.
© 2025 PatSnap. All rights reserved.Legal|Privacy policy|Modern Slavery Act Transparency Statement|Sitemap|About US| Contact US: help@patsnap.com