Heat sink and design method thereof and device and transformer
A design method and heat sink technology, applied in the field of transformers, can solve the problem that transformer heat sinks cannot meet the requirements of heat sink volume and heat dissipation efficiency, etc.
- Summary
- Abstract
- Description
- Claims
- Application Information
AI Technical Summary
Problems solved by technology
Method used
Image
Examples
Embodiment 1
[0038] In this embodiment, a method for designing a heat sink of a transformer is provided, which is used to design the optimal size of a heat sink in a transformer, wherein the optimal size refers to the external size, heat dissipation, maximum temperature rise and fan drive of the entire heat sink Under the condition of given power, the radiator structure is optimized to minimize its volume or mass.
[0039] The structure of the heat sink is as figure 1 As shown, the meanings of the dimensions represented by each letter are as follows: L and W are the dimensions of the heat sink base, δ indicates the thickness of the fins, z indicates the spacing of the fins, b indicates the height of the fins, A p Indicates the cross-sectional area of the fin in the direction of heat conduction. The purpose of the design method of the heat sink is to give the dimensions L and W of the base of the fin, and the air inlet temperature T m,i , susceptor temperature T s , then the base exces...
Embodiment 2
[0097] In this embodiment, a design device for heat sink is provided, such as image 3 shown, including:
[0098] The driving power calculation unit 01 is used to obtain the driving power of the cooling fan;
[0099] The air velocity calculation unit 02 is used to calculate the air velocity under different cooling fin pitches according to the driving power;
[0100] A target spacing calculation unit 03, configured to calculate the target spacing of the cooling fins according to the different spacings of the cooling fins and the corresponding air velocity;
[0101] The target number and target size calculation unit 04 is used to calculate the target number of cooling fins according to the height, and distribute the total heat to each cooling fin to calculate the target size of the cooling fins.
[0102] Wherein, the driving power calculation unit includes:
[0103] P N = u m zΔp
[0104] Among them, Δp represents the pressure drop of the air, z represents the distance betwe...
PUM
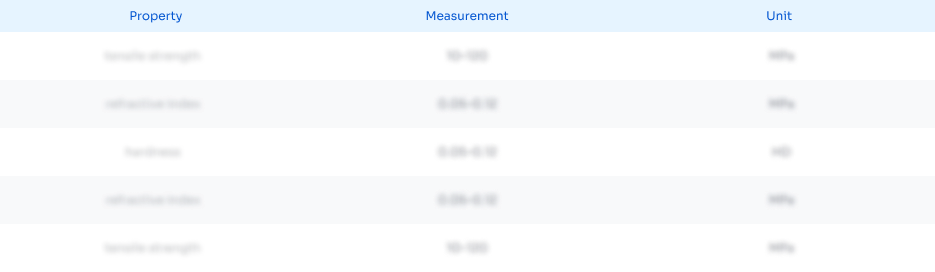
Abstract
Description
Claims
Application Information

- Generate Ideas
- Intellectual Property
- Life Sciences
- Materials
- Tech Scout
- Unparalleled Data Quality
- Higher Quality Content
- 60% Fewer Hallucinations
Browse by: Latest US Patents, China's latest patents, Technical Efficacy Thesaurus, Application Domain, Technology Topic, Popular Technical Reports.
© 2025 PatSnap. All rights reserved.Legal|Privacy policy|Modern Slavery Act Transparency Statement|Sitemap|About US| Contact US: help@patsnap.com