Device and method for testing axial dynamic rigidity of built-in machine tool spindles
A technology of machine tool spindle and testing device, which is applied in mechanical bearing testing, measuring device, testing of machine/structural components, etc., can solve the problems of difficult testing of spindle dynamic characteristics and difficult testing of machine tool spindle dynamic characteristics.
- Summary
- Abstract
- Description
- Claims
- Application Information
AI Technical Summary
Problems solved by technology
Method used
Image
Examples
Embodiment Construction
[0030]The present invention will be further described below in conjunction with the embodiments and accompanying drawings, but this should not be used as a limitation to the protection scope of the claims of the present application.
[0031] Built-in machine tool spindle axial dynamic stiffness testing device of the present invention (abbreviation device, see Figure 1-6 ) includes a force sensor sleeve 1, an axial displacement sensor 5, a front end device 6, a charge amplifier 7, a data acquisition card 8, a data processing terminal 9, a force sensor 10 and a magnetic base 11; the force sensor sleeve 1 is set on On the main shaft 4, and between the two bearings 2 at the front and middle of the main shaft, the force sensor sleeve 1 is in the shape of a ring, and on the inner side of the ring, there are four strain gauges 10 evenly distributed along the circumferential direction, corresponding to The force types of the two adjacent strain gauges are opposite, that is, one strai...
PUM
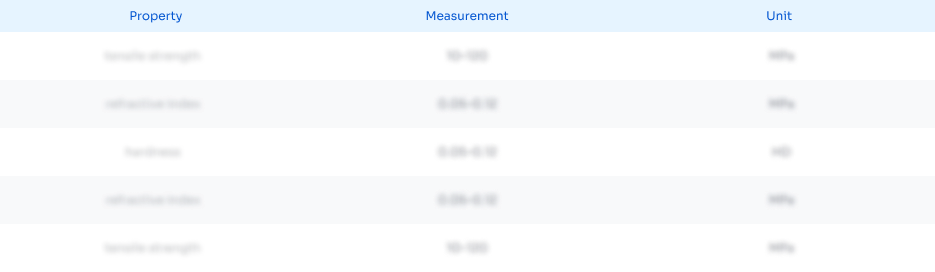
Abstract
Description
Claims
Application Information

- R&D
- Intellectual Property
- Life Sciences
- Materials
- Tech Scout
- Unparalleled Data Quality
- Higher Quality Content
- 60% Fewer Hallucinations
Browse by: Latest US Patents, China's latest patents, Technical Efficacy Thesaurus, Application Domain, Technology Topic, Popular Technical Reports.
© 2025 PatSnap. All rights reserved.Legal|Privacy policy|Modern Slavery Act Transparency Statement|Sitemap|About US| Contact US: help@patsnap.com