Assembly type filler wall system provided with steel frame and capable of achieving repositionable rigid connection and construction method of system
A rigid connection and rigid connection technology, applied in the direction of walls, buildings, building components, etc., can solve the problems of inability to connect, poor seismic performance, and heavy filling walls, and achieve easy assembly and connection, ensure construction efficiency, and easy to repair. Effect
- Summary
- Abstract
- Description
- Claims
- Application Information
AI Technical Summary
Problems solved by technology
Method used
Image
Examples
Embodiment Construction
[0050] Examples see figure 1 , Figure 6 , Figure 7 As shown, this prefabricated steel frame infill wall system includes steel frame columns 1 , steel frame beams 2 , prefabricated infill wall panels 3 , resettable rigid connectors 4 , flexible materials 5 , and plastering layers 6 .
[0051] see figure 1As shown, this prefabricated steel frame infill wall system with resettable rigid connection includes a rectangular steel frame surrounded by steel frame columns 1 and steel frame beams 2 and a prefabricated infill wall panel 3 filled in the steel frame. The upper end of the prefabricated infill wall panel 3 is connected to the upper steel frame beam 2 through a resettable rigid connector 4, and the lower end is welded and fixed to the lower steel frame beam 2; there is no connection between the prefabricated infill wall panel 3 and the left and right steel frame columns 1 , The gap distance between the two is 20mm ~ 30mm. see Figure 6 As shown, the gaps between the pre...
PUM
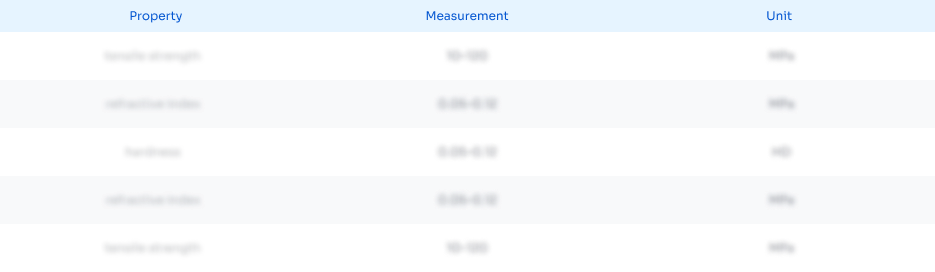
Abstract
Description
Claims
Application Information

- Generate Ideas
- Intellectual Property
- Life Sciences
- Materials
- Tech Scout
- Unparalleled Data Quality
- Higher Quality Content
- 60% Fewer Hallucinations
Browse by: Latest US Patents, China's latest patents, Technical Efficacy Thesaurus, Application Domain, Technology Topic, Popular Technical Reports.
© 2025 PatSnap. All rights reserved.Legal|Privacy policy|Modern Slavery Act Transparency Statement|Sitemap|About US| Contact US: help@patsnap.com